基于刚度和强度性能的新能源城市客车车身轻量化研究
- 来源:汽车科技 smarty:if $article.tag?>
- 关键字:新能源城市客车,车身骨架,轻量化 smarty:/if?>
- 发布时间:2019-08-21 07:22
摘 要:建立12米城市客车骨架有限元模型,以刚度和强度性能为评价基础,结合拓扑优化和尺寸优化的方法,并考虑生产及工艺要求,对车身底骨架进行结构和尺寸优化设计。研究结果及实车制造表明,轻量化效果显著,结构安全可靠,同时刚度和强度性能得到提升。该优化设计结果为同类车型的轻量化优化设计提供参考。
关键词:新能源城市客车;车身骨架;轻量化;优化设计
中图分类号:U463.82+2 文献标识码:B 文章编号:1005-2550(2019)03-0087-05
Abstract: The finite element model for a bus body frame of an 12m city bus is built, based on Stiffness and Strength Performances, combining with the methods of topology optimization and size optimization, considering with the actual production and process requirements, then the structure and size of the body understructure are optimized. The results show that the effect of weight loss is remarkable, safe and reliable ,at the same time, the Stiffness and Strength Performances of bus structure are greatly improved. The results also provide a reference for lightweight optimization design of similar vehicles.
Key Words: new energy city bus; body frame; lightweight; optimal design
以纯电动和混合动力为主的新能源城市客车已逐步替换燃油为燃料的传统城市客车。而续航里程是新能源汽车关注的首要问题。研究车身结构轻量化,降低整备质量,是汽车企业提高续航里程的主要方法之一。车身骨架是整车主要的承载部件,骨架质量在汽车整备质量中的比例占30%-40%,一般汽车轻量化主要是指车身结构的轻量化[1-3]。应用轻质材料、优化设计以及轻量化制造工艺是车身结构轻量化的三条主要途径。车身骨架轻量化优化设计主要是综合拓扑优化、形貌优化和多目标优化等结构优化方法来改变骨架的材料、结构和尺寸,在保证其性能的基础上实现减重的目的[4-5]。本文将介绍城市客车车身结构轻量化的研究方法和思路,为同类客车车身结构的轻量化设计提供参考。
本文选取一款成熟的12米铝合金车身纯电动公交车,车身骨架五大片为铝合金材料,而底骨架为传统的钢结构材料。应用铝合金材料后,整车已减重约560Kg。车身五大片骨架已经过材料轻量化(鋁合金)和结构轻量化的方法实现减重,现需要对车身底骨架钢结构部分进行优化设计,进一步发掘轻量化的潜力。现以实际车型的改进设计为实例讲解轻量化设计的方法和思路。
1 建模
在UG中建立整车三维CAD几何模型,再将模型导入到Hypermesh中,建立整车有限元CAE模型。如图1所示为白车身CAE有限元模型。
2 基于刚度性能的评价
设置相关计算参数及边界条件,借用OptiStruct求解器计算整车原始刚度性能参数。
2.1 弯曲刚度
如图2所示为集中力作用于简支梁时,其弯曲变形示意图。当客车车身作用有对称垂直载荷时,结构处于弯曲工况,其整体弯曲刚度可以有车身最大垂直扰度来评价[6-7]。此时客车车身骨架的整体弯曲刚度K为:
参照以上所述的弯曲刚度计算方法,结合实际情况,选择整车模型为研究对象,设置相关载荷及边界约束。经计算获得该车的整体弯曲刚度为:19.0×106N×m2。
2.2 扭转刚度
当客车行驶于不平路面上,车轮不同时碰撞到障碍物时,车身上受到左右非称垂直载荷的作用,车身结构处于扭转工况,产生扭转变形,此时客车车身结构应有足够的扭转刚度来抵抗变形[8]。一般计算前扭转刚度和后扭转刚度。
以前扭转刚度为例,流程:(1)选择整车白车身骨架为研究对象。(2)约束后悬左右悬架安装位置的中点。(3)在前悬架左右安装点施加垂直载荷,载荷大小数值相同方向相反。(4)利用左右悬架安装的支点Z向变形量计算整体的扭转刚度GJ,如式(3)、式(4)。
式中,δL是前悬架左支点的测点Z向变形量,δR是前悬架右支点Z向变形量,T是施加的载荷,X是后悬支撑点到测点的距离,B是左右施力点的间距。
根据以上方法,获得该车的前扭转刚度为:9.11×106N×m2/rad。同理后扭转刚度为:
8.32×106N×m2/rad。
3 基于强度性能的评价
3.1 载荷提取
在HyperWorks 软件的多体仿真模块 MotionView中建立前、后悬架系统模型,通过添加工况条件和输出项,计算悬架系统施加在车身上的作用力及力矩,为静强度分析提供载荷输入[9-10]。
因此,在MotionView中建立前、后悬架系统模型,结合实际情况,对各工况设置不同参数,计算获取悬架系统与车身连接点的载荷。
流程:(1)根据实际情况简化模型。(2)借鉴MotionView模型库中的模型,选择相应的模型模板,在此基础上改进模型。(3)建立前、后悬架动力学模型。(4)校核模型、整车参数及工况设置。(5)求解计算。(6)仿真结果后处理。如图3所示为弯曲工况下载荷示意图。
3.2 强度数据
客车的使用工况是很复杂的,主要考虑使用过程中满载弯曲、极限扭转、紧急制动、急转弯等典型工况。在各工况下,骨架最大应力需要小于材料的疲劳强度或屈服强度。结合以上方法,建立整车有限元模型,根据实际情况对整车骨架进行配载。借助HyperWorks软件,对车身骨架施加MotionView中获取的边界载荷,进行静态强度分析,考察车身骨架的强度性能[11]。
载荷处理:按照实车情况进行配载,配载后模型重量加簧下质量达到整车最大设计质量。边界约束:把MotionView中获得的载荷输入到强度计算模型中,利用惯性释放的方法计算车身骨架在各工况下的受力情况。
需要保证各工况下整车应力水平需满足材料的疲劳强度或者屈服强度。通过计算分析,车身骨架变形和应力均在允许范围内,并验证本次建模的正确性。
4 基于強度和刚度性能的结构优化方法
4.1 拓扑优化方法
车身骨架的拓扑主要采用变密度法进行优化设计,通过查看材料密度,得到结构的最佳布置方式[12]。
优化过程是一个不断寻优的过程,因此选取可优化区域,分阶段拓扑,最终达到减重目的。本车底骨架斜撑、纵梁、加强梁等位置是拓扑寻优的重点区域。
流程:(1)定义拓扑优化区域。保留底骨架主要的横梁和纵梁,删除斜撑、加强梁等,用同等质量壳单元的平板来替代该区域。(2)定义响应。定义拓扑区域的质量分数和整车各强度分析工况加权值为拓扑分析的响应。(3)定义约束。把(2)中定义的质量分数设置上限约束。(4)定义目标。定义强度分析工况加权值的最小值作为目标。(5)计算求解。图4所示为中段底骨架拓扑优化结果。
根据拓扑优化结果,结合实际设计、工艺、生产进行调整。调整后重新计算拓扑优化设计后车身骨架的刚度性能数据,需要保证优化后的骨架弯曲刚度、扭转刚度值不可低于原始值,最终确定出合适优化方案。
4.2 尺寸优化方法
在尺寸优化设计中,模型有了初步的几何形状、材料类型、拓扑结构后进行的细节设计,它通过改变结构单元的塑性,如壳单元厚度、横截面积等达到一定的设计要求[13]。
经过拓扑优化,对底骨架结构进行了重新优化设计,已达到一定的减重效果。为更进一步挖掘轻量化的潜力,对结构进行灵敏度分析,寻求最优的梁结构尺寸。同拓扑优化类似,选取可优化区域,分阶段尺寸优化,最终达到减重目的。
流程:(1)定义设计变量。对需要尺寸优化的梁定义为设计变量,优化选择的厚度需要考虑结构和工艺上的可行性。(2)关联设计变量与梁单元属性之间的关系。(3)定义响应。将所有需要尺寸优化的梁定义质量响应及整车各强度工况加权值响应。(4)定义约束。如对优化区域的质量、单元应力定义上限约束。(5)定义目标。定义各强度工况加权值的最小值为优化目标。(6)计算求解。如图5所示为中段底骨架尺寸优化结果。
结合实际情况对尺寸优化后的结构进行调整。调整后重新计算优化设计后骨架的刚度性能数据,需要保证优化后的骨架刚度值不可低于原始值,最终确定出合适优化方案,得到最终模型和减重值。
4.3 优化效果及现状
经过拓扑优化和尺寸优化,结合生产、工艺等实际情况,获得优化后的结构模型。对优化后的模型进行刚度和强度性能分析,对比前后性能的变化。优化设计后理论上减重约186Kg,如表1所示为轻量化前后性能对比表。仿真结果表明,优化后的车身骨架的性能参数略有提高,强度分析也满足材料设计使用要求,从而验证了本次轻量化设计的合理性和有效性。
将优化后结果输出成相应设计及生产文件资料指导实际车型的轻量化结构设计和生产制造。如图6所示为实车制造后照片。对比前后二批同配置纯电动公交车过线数据,最终实车可以减重178Kg,在误差范围内基本同理论减重数据相符。
当前,优化设计后的纯电动公交车已生产制造出400多台,服务于国内大中城市。经过市场运行检验反馈,该车型性能优越,结构安全可靠,整车质量暂无发现问题。
5 结束语
本文选取12米城市客车为研究对象,建立车身骨架有限元模型,以刚度和强度作为性能评价的基础,结合拓扑优化和尺寸优化的方法,并考虑实际生产及工艺要求,对车身底骨架进行结构和尺寸优化设计。研究结果及实车制造表明,轻量化效果显著,结构安全可靠,同时车身骨架的刚度性能得到提升,各工况强度性能也满足设计要求。该优化设计结果为同类车型的轻量化优化设计提供参考。
参考文献:
[1]牛妍妍.新能源客车轻量化技术路径研究[D].长春:吉林大学,2016.
[2]徐志汉,王泽平.纯电动城市客车车身有限元分析[J].客车技术与研究,2015(3):11-13.
[3]刘显春.纯电动客车车身骨架多目标轻量化设计[D].合肥:合肥工业大学,2015.
[4]毛爱华.纯电动大客车骨架结构轻量化多目标优化设计[D].长春:吉林大学,2015.
[5]黄石华.基于刚度特性的车身结构轻量化研究[D].长沙:湖南大学,2011.
[6]赵振垒,洪金怀等.客车车身静刚度计算及测试方法研究[J].客车技术与研究,2017(6):48-51.
[7]那景新,何洪军,闫亚坤.基于统计处理的车身弯曲刚度计算方法[J].吉林大学学报,2011,9:21-23.
[8]王丹阳.承载式客车车身结构刚度计算,方法研究[D].吉林:吉林大学,2009.
[9]高玉聪.客车空气悬架多体性能仿真分析[D].西安:长安大学,2013.
[10]王东元.大客车空气悬架多体动力学及模态分析[D].西安:长安大学,2015.
[11]沈光烈,谢义杰.惯性释放法在车辆有限元分析中的应用及缺陷[J].客车技术与研究,2016(5):1-3.
[12]姜卫远.基于拓扑优化的电动汽车先概念车身设计方法研究[D].北京:北京理工大学,2015.
[13]冶志亮.基于被动安全性的轿车白车身结构轻量化设计[D].长春:吉林大学,2017.
林标华
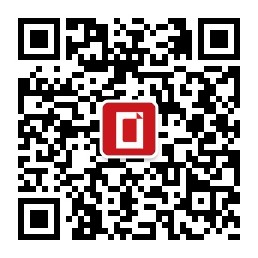