饮料厂渴求自动化
- 来源:国际食品加工及包装商情 smarty:if $article.tag?>
- 关键字:饮料厂,自动化,生产 smarty:/if?>
- 发布时间:2024-03-09 20:38
作者:Pan Demetrakakes
摘自Food Processing 杂志
饮料厂的自动化正面临更大挑战。他们通常将慢速批量生产与高速灌装和其他包装操作结合在一起,因此很难进行协调。
高速运转的包装设备往往容易出现故障,这使之与加工过程的协调变得更加复杂。贸易客户对包装模式的定制化和精细化要求越来越高,具有高度灵活性的设备才能满足这些需求。
饮料自动化所面临的挑战既有日常考虑的因素,如保持系统运转、防止中断失控,也有更宏大的挑战,如将数据情景化,用于预测性维护和其他目的。要应对这些挑战,需要将机械和数字战略结合起来。
饮料厂(以及许多其他工厂)自动化最基本的功能之一就是防止出现基本错误,例如产品与包装不匹配。GraySolutions 公司业务开发总监 Raymund Alfaro 表示,这些错误经常发生,原因很简单,就是操作员没有注意到。
为此,该公司对客户自动化系统进行改进,新系统可以读取即将灌装的容器上的标签,并确保与灌装机中的产品相匹配。
Alfaro 说,在许多情况下,保持系统正常运行只需建立足够的吸收能力。这种装置应该位于最容易发生中断的包装设备(如装盒机或装箱机)的上游。通常采用台式或堆叠式蓄能器的形式,以便在解决下游问题时收集罐子或瓶子。
有时,超长传送带也能起到作用。Alfaro 还记得俄亥俄州的一家工厂,它的传送带长达一英里,以消化积压的货物。
空间是宝贵的
但是,由于公司希望节省空间,因此越来越多公司不选择长输送机,建筑和施工公司 CRB Group 包装工程师Brigadare Manradge 说道。
Manradge 说:“饮料行业并不一定要使用更多传送带,因为这会占用更多宝贵空间。一个主要的驱动因素是,如果是新建项目,则要尽量降低初始投资成本;如果是棕地项目,则要将更多面积用于实际生产。”
常见做法是为特定的 SKU 配备单独传送带,通常由不同的灌装机组成。这些传送带上的闸门或其他分流装置可将正在装箱或码垛的 SKU 重新输送到不同生产线末端设备。然而,在需要频繁更换 SKU 的情况下,这种方法就不那么奏效了。多年来,随着大型贸易客户越来越多地要求对箱装甚至 6 包或 12 包的产品进行定制混合,这一直是个问题。
末端包装设备供应商 Serpa 包装公司销售和应用总监Aaron Metzler 说:“我认为目前的挑战在于多品种多口味产品的包装,然后,市场营销人员希望瓶体能按特定顺序和特定方式装入纸箱。”
在这种情况下,自动化可以发挥作用。在以相对较高的速度进行各种包装时,机器人可以将瓶体分离出来放入积放区,然后根据需要将它们送回通道。
数字化
当然,与自动化有关的许多挑战和机遇都与数字信息有关,即如何存储、传输、接收和使用信息。
最基本的使用形式可能是人机界面(HMI)——让车间操作员控制设备的软件。很多时候,操作人员,尤其是资历尚浅的操作人员,很难解读他们所操作设备的人机界面。
Manradge 说:“实际上,大多数客户都希望人机界面能与技术背景较弱的年轻员工有更多互动,这样他们就能了解设备问题所在,并能快速修理设备。”
他补充说,问题的部分原因在于,许多人机界面是由工程师设计的,他们没有与现场任何操作人员一起工作过,而这些操作人员可能没有工程学位。因此,有时对问题的描述非常工程化,操作员很难理解。
操作员与机器之间以及机器与其他在线设备之间的通信问题是自动化的核心。随着设备自我诊断能力的提高,传输和使用数据的能力也必须随之提高。
一般来说,设备在出现问题时具有较高指示能力。这一点对于包装设备尤为重要,因为包装设备通常使用许多必须相互协调的运动轴,其中一个轴的失灵会导致整个机器停止运转。
生产线末端包装设备供应商Somic 公司首席执行官Peter Fox 说,有时包装设备也能追踪生产线其他地方的故障情况。Somic收集有关正常运行时间、机器故障、故障原因和整体运行效率的数据。我们的客户通常使用这些数据来确定整个生产线的效率,因为我们通常是生产线的末端。“因此,我们可以收集上游设备停机或故障导致的‘等待产品’等数据,”Fox 继续说,“我们的系统提供饼图和其他图形输出,以此帮助工厂快速评估生产线的性能。”据Serpa 公司电气工程经理Jon Gaiser 介绍,可以从Serpa 设备中提取的数据类型包括:警报:用于生成历史和预测性维护,并确定停产原因;统计数据:用于生成趋势分析生产报告;设备状态:用于查看生产线上的设备在生产过程中处于何种状态。
标准化是关键
要使这些数据发挥作用,就必须在整个系统中随时可用并保持一致。自动化也是同样的道理——数字控制的标准化是关键。罗克韦尔自动化公司战略业务经理 MatthewHansen 表示,遗憾的是,这并不容易实现,尤其是在对现有设施进行改造的棕地项目中。
Hansen 说:“在尝试协调和集成整个工厂(特别是棕地工厂)时,面临的主要挑战之一是来自不同供应商的各种不同年份的控制和自动化设备。这可能会导致多种网络类型、通信协议、数据类型和数据命名约定,而这些往往会导致数据的非结构化和不同步。”
另一项要求是信息架构——传递信息的软件结构。最常见的是机械设备通常通过 PLC 向 SCADA(监控和数据采集)系统或 MES(制造执行系统)等直接监管层提供数据和接收指令。这种软件通常会反过来向更高层提供数据和指令,在某些情况下,还可应用于 ERP(企业资源规划)系统。然而,罗克韦尔通用互联应用总监 Achim Thomsen表示,现代加工和包装设备不断提高的信息技术能力有可能颠覆这种传统结构。他说:“虽然与 MES(最终与 ERP系统集成)连接的工厂车间控制一直是制造业公认的架构,但随着边缘通信技术的出现,我们可以考虑更优化的替代方案。”
边缘计算是指内置控制和诊断功能的“智能”设备,而不是通过 PLC 或其他控制器工作。结合设备通过互联网(“工业物联网”或 IIoT)进行控制或监控的能力,这有可能取代传统的控制软件架构。
Thomsen 将此称为“软件定义的制造”,并表示它为车间级数据的关联和使用提供了更多机会。他说:“MES将不再是一个‘系统’,而更像是整个制造基础设施中的一套同步服务。MES 服务的作用和重要性将会增加,用户将能获得与其有效需求相关的MES 技术的更优化组合。”
饮料厂的自动化尤其具有挑战性,因为这通常涉及到高产量和高速度。信息技术的创新有可能超越这些挑战,将饮料生产效率提高到一个新的水平。
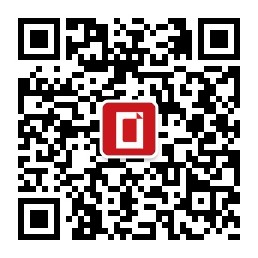