多工序加工系统的数控夹具设计
- 来源:中国高新科技 smarty:if $article.tag?>
- 关键字:多工序加工,数控技术,夹具设计 smarty:/if?>
- 发布时间:2020-01-04 08:28
摘要:在现代制造系统中,夹具会对零件的加工质量与效率带来直接影响,可以创造出更高的效益。文章以多工序加工系统为基本背景,对其中的数控夹具设计展开探讨,分析其应用状况,以期给同行提供可行的参考。
关键词:多工序加工;数控技术;夹具设计
文献标识码:A 中图分类号:TG659
文章编号:2096-4137(2019)22-28-03 DOI:10.13535/j.cnki.10-1507/n.2019.22.07
0 引言
计算机辅助夹具(CAFD)涉及方面众多,最为典型的有夹具构形、定位方案等方面的设计工作。计算机辅助工艺设计(CAPP)也是多工序加工系统中的重要部分,具体表现在工艺改良、自动化等多个层面。在展开多工序加工时,工程人员提出了一系列方法,常见有单位向量法、矢量判别法等,为现代数控夹具的发展创设了良好的条件。基于可行的装夹方案,在确保产品质量的同时可明显缩短加工时间,全方位实现具备多工艺、多工位特性的加工效果。
1 多工序加工系统中数控夹具设计问题
1.1 装夹工件总量问题
在展开夹具设计时,为满足施工效率要求,需适当提升装夹工件数量,此方式避免了换刀麻烦,改善了传统方式下停机频率高的问题。
1.2 夹具定位问题
数控机床加工对精度提出较高要求,意味着夹具定位工作尤为重要。在数控编程过程中,必须保障工件达到夹紧状态,同时准确定位在夹具上,创建工作坐标系,将其中的原点作为基本点,用于安装夹具,对应于机床坐标系中,则有一个准确位置,机床坐标系原点与该位置存在偏差,可体现在X、Y、Z 3个方向上,而这正是“对刀”,具体的值可基于G54~G59得到。结束“对刀”作业后,便为数控加工程序运行创设了条件,同时机床坐标与工作坐标也存在对应关系。
1.3 更换问题
为控制工程成本,创造更高的效益性,需要注重对系列产品的设计,在结构、尺寸等方面普遍存在相适性,因此要考虑夹具通用性问题,使夹具适用于某一系列的多个产品加工。考虑到夹具定位精度要求,必须保障夹具体孔与定位件外圆的配合关系,二者不可产生间隙,且要严格控制过盈量,否则会加大零部件更换难度。基于此,在前期设计时较为可行的是过渡配合。此外,有必要在定位件中心增设螺孔,将螺杆拧入其中,提升定位件拆卸便捷性,基于轻松操作便可被顺利顶出。
1.4 夹具刚性需求问题
在编制数控加工方案时,最为基础的是工序集中原则,这点在夹具设计过程中要进行充分考虑,满足高刚性要求。部分情况下,粗加工与精加工均对应于相同夹具,若此条件难以与数控加工相适应,则要注重对夹具设计思路的调整,以满足实际加工需求。
1.5 其他问题
事实上,夹具设计是一项系统性工作,在尽可能减少元件使用量的同时要最大程度上提升刚度,做好夹具定位工作,确保各定位面对应机床坐标中都能寻找到具体的点;此外,设计者要充分考虑夹具与机床的布置问题,彼此不可出现空间干涉现象。2 数控加工夹具的要求
为提升数控加工品质,对夹具提出较高要求,设计过程中要注重效率、适用性与精度3大原则。要充分考虑夹紧力、作用点等相关因素,在展开加工作业时,考虑工件所处位置及生产需求,由此确定夹紧装置的具体类型,如自动型或是手动型等。在操作之前展开限位尺寸检查,看其所处位置是否准确,若采用自动夹紧装置,生产中提出了夹紧动作迅速的要求,同时要具备充足夹紧力,但此过程不可对工件定位造成不良影响。关于手动夹紧装置,需设置自锁功能,同时满足结构精简的基本原则。受装配方式不同的影响,所带来的夹具制造公差自然也存在一定差别。在整体夹具设计工作中,需考虑当前行业内广泛使用的标准件与通用件,为提升后续维护的便捷性,在最大程度上控制专用件的使用频率,所使用的工件要满足通用性要求。
3 数控加工夹具的优点
多工序加工系统之所以得到广泛应用是因为存在诸多优势,具体表现在:
(1)优良的精度标准,分析数控机床特性得知,具备连续多型面加工的丰富功能,为满足运行需求,对夹具精度与刚度均提出更高要求,在整体条件相均衡的背景下,可控制粗加工误差等问题。
(2)定位准确,相较于夹具而言,工件处于完全定位状态,且夹具在机床上依然达到了完全定位状态,各夹具都对应于机床坐标,在确保定位精度的同时可达到简化定位的效果。
(3)空间优势,可以在同一时间顺利完成多个工件表面安装作业。
(4)便捷化调整,适配了快速更换程序,避免传统方式下更换工装耗时长的问题,这对于贵重设备而言尤为关键,可大幅缩减此类设备等待时间,通过快速调整的方式便可在短时间内达到更换工件的效果,以推动后续生产加工的持续开展,适配了高性能转动机构,即便是机动时间依然可以完成夹具更换操作,突破了过去停机更换且耗时长的限制。
4 数控加工夹具的设计要点
分析数控加工夹具的构成,主要可拆解为定位装置、夹具体与夹紧装置3个。在展开夹具设计工作时,需充分考虑效益性、智能性及适用性的基本原则。赋予夹具设计更高的内涵,它涉及到各零件加工信息,以工件质量为指导,得到合适的零件尺寸,分析并确定形位公差,综合考虑夹具材质与结构特性,可形成夹紧方案,加之三维建模装配图等辅助信息,可得到最终方案。探讨加工精度极具必要性,基于夹紧力实现对工艺装备的可行性验证,在此基础上得到夹具装配图,综合各类因素可得到完善设计方案。在展开夹具设计时,需注重如下几点内容:
(1)提升夹紧装置所处位置的精确性,保障夹具的适用性,为数控加工程序的运行创设稳定条件;
(2)分析夹具的实际需求,并考虑受力部件应满足的刚度与强度指标;
(3)增强夹具通用性,通过可行的方式规避过去夹具旋转过程中引发的质量失衡问题,增强施工安全性,创造更高夹具利用率;
(4)合理规划机床与夹具,二者在运行过程中不可出现相互影响的现象,同时夹具尺寸的高度要满足特定精度要求。
5 数控夹具的主要分类
夹具主要分为以下几类:
(1)铣床夹具。
(2)通用夹具。不需要调整就可以加工很多不同的工件,设计标准成熟,具有很强的灵活性。
(3)专用夹具。根据工件特征,为满足客户大批量订单生产需求而专门为某个产品的某道工序设计的夹具,操作便捷,但缺乏柔性,且一旦修改产品形状和尺寸,夹具就不能继续使用。
(4)钻床夹具。
(5)组合夹具。设计和组装周期短、使用寿命长、能加快工件加工的周期、投入成本低、可重复多次使用、使用范围广,组合夹具包括可调部分和基本部分,适合于在形状与尺寸上有所变化的多种工件,使用时可更换和调整,但元件之间不能实现互换,所以在一定程度上会影响工件的加工精度。组合夹具是目前机床夹具中通用化标准化程度最高的一种夹具,在数控加工没有专用夹具的情况下,可用组合夹具代替。
6 数控夹具的设计过程
齿轮减速箱体加工夹具设计案例如图1所示。
6.1 定位装置的设计
在整个夹具构成中,定位装置是尤为重要的部件,有别于普通机床的是,此时定位工作基于夹具而完成,围绕零件自由度问题展开探讨,确定工具几何要素关系,充分考虑到点、面、中心线3部分因素,从而控制定位误差,以减速器箱体零件为基础,进而展开建模操作,创建夹具元件库,在建模过程中可灵活调用。以圆形构件定位心轴为基准,在此基础上适配3个杠杆压板与1个定位块,利用上述元素构成定位夹具零件,借助三维软件创建模型,具体如图2所示。
图2 夹具零件
6.2 夹紧装置的设计
在设计装置时,出于提升夹具质量的目的,要以零件误差分析结果为基准,进而探讨加工切削力问题,挑选可行夹紧元件并融入至装配图中,综合分析夹紧元件尺寸及所处位置,分析是否有必要对既有方案作出更改,以得到全新的定位夹紧方案,提升设计图纸的直观程度。
6.3 干涉检查、装配基准和结构可调性
结束夹具整体设计工作后,围绕零件、工序结构等问题展开干涉检查。为保障整体设计质量,最为基础的是刀具与夹具的空间规划问题,彼此之间不可干涉。综合大量设计经验,围绕夹具装配加工展开仿真模拟操作,通过此方式可较为准确地分析夹具元器件的干涉问题;同时,夹具要利用销钉等零部件进一步固定,若存在调整夹具的需求,借助调整垫圈可实现。基于对固件元件修磨的方式,也能达到补偿其他元件误差的效果,确保夹具精度。
本夹具采用一面两销定位,限制5个自由度,保证定位准确性;夹紧方式采用杠杆式压板压紧,可增大压紧力,使零件加工增加稳定性,压紧牢固。
6.4 减速箱零件装夹力分析
根据所设计夹具,使用SolidWorks软件Simulation Xpress有限元分析模块进行应力分析。对减速箱体增加外部载荷,零件材料为铸钢,铸钢屈服应力2.482e+004N/m2,虽然红色部分为3.502e+004N/m2,远远<能承受的屈服应力。零件位移情况,从受力面往下,位移量越来越大,但是位移量最大值只有3.069e-005mm,小到可忽略不计。有限元分析结果显示零件是安全的。通过应力分析结果可知,在零件装夹时,压板不能靠近图3的弯曲部分,尽量在夹紧前提下靠近零件边缘,否则零件变形。
图3 减速箱零件图
夹具使用手工装夹上下料,在底板两边预留凹槽用于上下料接口,可使用上料机械手进行零件装夹;零件采用四轴伺服旋转台1次装夹,完成多面的加工,确保加工精度,保证加工尺寸的一致性,提高加工效率。
7 结语
数控夹具在长期发展下,已经成为多工序加工系统的关键,多数公司高度重视该技术。在其作用下,可改善零件精度不足问题,提升加工效率,控制成本,为企业带来良好效益。
参考文献
[1] 平艳玲.数控加工中的工艺与夹具设计若干问题研究[J].设备管理与维修,2019(6):158-159.[2] 黄渊莉.数控加工中的工艺与夹具设计[J].数字通信世界,2018(12):240.
广州市交通运输职业学校
辛 健
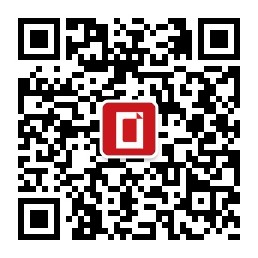