增材制造:风口之下,现状如何?
- 来源:国际金属加工商情 smarty:if $article.tag?>
- 关键字:展期,发展现状,造型模型 smarty:/if?>
- 发布时间:2020-09-09 09:06
经过 7 月 8-10 日三天的精彩展期,第六届亚洲 3D打印、增材制造展览会 TCT ASIA 2020,终于在上海新国际博览中心落下帷幕。
在 TCT 亚洲展举办的同期,TCT 科技讲台与亚洲峰会,也如约和观众见面。来自上汽大众、东风汽车、一汽大众、空中客车和成立航空等众多 OEM 厂商以及来自复旦大学、空军工程大学和中国航空制造技术研究院的专家们分别从应用和学术等不同方向为观众介绍了增材制造在不同领域的发展现状以及存在的问题。
3D 打印技术起源于上世纪 80 年代末,它的出现颠覆了传统的制造技术。由于其集概念设计、技术验证与小批量制造于一体,为缩短汽车设计研发的后期,提高新产品的成熟度,快速推出新车型,降低产品开发成本和全新设计理念的汽车研发提供了高附加值的可能。
目前在汽车制造领域,3D 打印技术可用于:前端产品研发,工装的夹具、检具制造和个性化定制和改装。
造型是产品研发最前端的环节,传统的造型模型有一个缺点,那就是与实车效果相去甚远,这导致造型的效果大打折扣。使用 3D 打印技术,保证了造型模型可以做到和实车一模一样,从而更好地评判造型效果,确定造型方案。
另外,3D 打印技术在产品研发中还被大量运用于零件的结构设计和技术验证。一个简单的例子——汽车座椅,如何既舒适又保证强度?我们在前期做好一个方案之后,马上通过 3D 打印技术做一个样品,通过样品来评价。这样的结果是模具工装的投入降低,同时把制造的时间缩短70%,还能减重 15%,优化的设计更是提高了产品的成熟度。
3D 打印技术也在颠覆车身设计的思维。比如说在传统的制造工艺下,一些圆角是没法做出来的,但是 3D 打印技术就可以完美地解决这些问题。一些以前制造所不敢想象的毛坯件,还有轻质材料都可以用 3D 打印来替代传统工艺来解决。
3D 打印用于工装夹具和检具的制造。我们长沙的总装工厂就曾经碰到一个问题,怎么快速去控制平整度?这个时候用传统的三坐标测量机是无法完成的,我们就想到了用 3D 打印技术做几个快速的非标检具,很快就解决了问题。可以说,只要掌握 3D 打印这门技术,就可以把它应用在各个方面,不一定是产品研发,还可以用在制造部,甚至还可以用在设备维修方面。
3D 打印技术用于个性化定制。比如说打印一些的客户喜欢小玩具放在仪表盘内,只要零件不是安全件,都可以做,从接受客户的订单到交货一般都能在一周内完成。
对于有兴趣尝试 3D 打印技术的汽车制造商来说,如何实现增材制造从概念到可以被安装在实车上的一个个零件的进程?这里我们可以参考戴姆勒的三步走的策略。第一步是在一个庞大的零件的数据库里面,分析、找到适合于 3D 打印的零部件;第二步是概念验证,验证筛选出来这些零件,在经济性以及技术方面是不是可行?第三步就是利用 3D 打印来实现数字化的零部件生产。
综上所述,现在通过 3D 打印技术,我们可以实现汽车工业的高附加值的应用,关键是我们一定要学会怎么去利用这样一个先进的技术。
随着技术的发展 , 近年来 3D 打印技术在医疗器械领域已获得应用上的突破。这主要是因为个性化医疗需求日益显著 , 而在市场上鲜有标准化量产产品 , 而 3D 打印体现出来的个性化、小批量和高精度正好满足了这一需求。
目前 3D 打印在生物医药中的应用主要有:骨科、齿科、器官和组织以及生物传感器几个领域。其中,骨科和齿科已经是 3D 打印发展较为成熟的两个领域。
3D 打印解剖模型在骨科手术的使用已被广泛证明是有益的。在脊柱手术治疗中,最重要的是准确置钉,减少手术并发症,颈椎的椎弓根细小,置钉难度大,手术过程易出现并发症,而 3D 打印的导板能有效解决上述问题。导向器辅助下的椎弓根定位准确,使用方便,可减少螺钉的偏离。在脊柱侧弯的手术中,3D 打印机可视化技术更能直接测量畸形的角度,分析螺钉植入的最佳方案。
对于骨科植入物来说,模仿骨骼的特性使其在体内的利用率最大化非常重要,而 3D 打印的金属细胞支架如下的特性是模仿骨骼性能成为可能:具有生物相容性能使支架上的细胞自然生长,在植入区域与现有的组织具有机制相似性、有适当的孔隙率给细胞提供适当的营养以及废物的传输通道、拥有能吸引细胞附着及在其表面生长的表面形态。
齿科 3D 数字化解决方案利用模型及口内 3D 扫描技术采集数据,通过齿科 CAD 软件输出设计,最终通过光固化3D 打印技术生产工作模型、正畸模型、种植模型、种植导板、蜡型冠桥、支架等,或利用金属 3D 打印直接打印金属冠桥和支架,制作固定活动的修复体。
毫无疑问,3D 打印技术给齿科带来了更高精度、更低价格的产品。但也应该看到,打印材料是在牙科领域推广应用的瓶颈。目前在牙科市场上应用最为广泛的制造材料有以下几种:陶瓷、钴镉合金、树脂、氧化锆、钛合金等。目前仍未有和人体牙齿各项性能均匹配的材料,未来或许在材料的探索中仍存在潜力。人体器官的坏死和病变等引发的器官移植一直是临床的一大难题。一方面,找到合适的捐献器官并不容易;另一方面,来自不同个体的器官容易引发不同程度的排斥反应,最终导致植入失败。因此,人工制造复合需求的人体组织器官是临床亟待突破的问题;以特定组织的功能细胞或多功能干细胞结合定向分化诱导因子作为“墨水”,打印出一层细胞组织结构,随后采用 3D 成型技术进行制造,层层叠加,最后形成立体的细胞组织架构,也就是临床所需的人工组织和器官。
生物传感器简单来说,就是将生物敏感物质的浓度转化为电信号的一种检测仪器。它能实现对人体内一些生物活性物质,如酶、抗体、抗原、微生物、细胞、核酸等的“即时检测”(POCT)。
未来十年,生物传感器的发展不再是像智能手表或者健身手环那样,而是通过 3D 打印技术实现的个性化需求。常用的生物传感器 3D 打印技术包括挤出、光固化打印及喷墨打印。
对于大国空军来说,单个基地动辄数千架飞机,老型号、小批量或引进装备的保障成为一大难题。无论美国、俄罗斯还是中国空军,都面临着配件 / 备件短缺、传统制造成本过高等问题。而针对这一系列问题,快速反应的增材制造技术几乎是最优选择。
但是,应当看到,任何高科技的产品 / 技术在使用、发展到一定阶段后都会面临一个死亡陷阱。如果它不能得到大众的接受以及进一步扩大其应用范围,那么它很有可能就会面临着“死亡”的命运。
而增材制造现在正面临着这样的命运:
首先,增材制造的核心技术有待突破。增材制造的核心包括原材料、制造设备、设计和工艺软件。
①原材料主要有:金属粉末、液态光敏树脂、高分子颗粒等,不仅种类有限,且制造的精度、复杂性、强度都亟需提高,目前国内使用的高端原材料都只能依赖进口;
②制造设备的关键器件,如激光器、扫描振镜、喷头、精密光学器件等大部分都来自进口;
③制造设备的性能也有待提高,尤其在精度、速度和效率稳定性方面;
④目前主流的设计软件(如 Solid Works、UG、ProE、AutoCAD)和工艺软件(如 Magics 和 Minics)基本由国外垄断。这些因素导致目前增材制造应用价格昂贵。
其次,相关行业标准体系不健全。增次制造技术发展迅速,然而已发布的标准却非常有限。由于没有标准规范,即使用同一个三维模型,不同生产商设备制造的产品都不尽相同,这使得该技术的大范围推广使用受到了制约,
再次,材料和产品性能有待认证或鉴定。增材制造技术作为一项新技术,其产品性能、质量、精度、可靠性等方面都备受质疑,即使是同一台设备在不同环境下打印出的不同批次的产品都有可能存在差异。3D 打印技术的可重复性和环境适应性都有待进一步提升。
最后,增材制造技术数据库远未建立。增材制造是建立在三维建模基础上的,每个产品都有对应的三维模型数据。要实现装备现场的快速维修,需要有相应的数据库支撑。这个数据库需要装备、研、产等多方支持,而航空装备的种类很多,零配件型号各异,建立数据库的工作量并非一朝一夕可以完成。
马珺
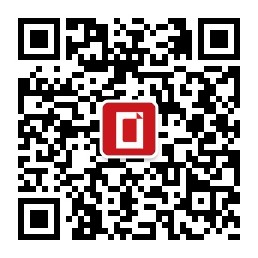