液压同步提升技术应用于岸桥加高工程的设计要点
- 来源:中国高新科技 smarty:if $article.tag?>
- 关键字:液压同步提升,岸桥加高,开关阀 smarty:/if?>
- 发布时间:2021-02-14 11:10
摘要:文章主要结合集装箱码头岸桥加高实际项目中所采用的液压同步提升装置,分析了基于钢绞线承载的液压同步提升装置的设计要点。
1 同步液压提升技术在岸桥加高工程的应用背景
上海振华重工(集团)股份有限公司是重型装备制造行业的知名企业,主要生产大型集装箱机械、散货装卸机械和其他产品,如大型钢桥等。近年来,公司注意到了岸桥改造市场特别是加高改造市场的巨大需求,在这方面投入了专门的技术团队力量。不仅给码头用户提供岸桥加高改造的产品改造方案,也给码头用户提供岸桥加高的具体施工过程的技术实施方案。从进入岸桥加高改造市场以来,已为国内外的码头用户实施了超过100台岸桥的加高改造。为顺利完成岸桥的加高施工,公司先后开发了3套加高装置:基于链板式承载的液压同步提升加高装置、基于多顶升料块式承载的液压同步顶升加高装置和基于钢绞线承载的液压同步提升加高装置。本文将主要分析基于钢绞线承载的液压同步提升加高装置。
2 钢绞线液压同步提升系统组成
钢绞线液压同步提升系统主要由以下部分组成:提升油缸总成8只、泵站总成4台、主控柜1台、地锚8只、外部连接软管48根、连接电缆若干、控制电脑1台。
各部件连接组成方式为:1根动力总电源电缆连接至主电控柜,主控柜分4路动力电源电缆至4台泵站,每台泵站有两根信号电缆分别至左、右两只提升油缸,每只提升油缸总成有6根软管连接至泵站,其中4根用于上、下锚定油缸,2根用于主提升油缸;控制电脑与主电控柜之间采用网线通信,主电控柜与4台泵站之间采用Profibus-DP通信。
一个提升油缸总成集成了上、下锚具油缸各4只;上、下锚感应限位各4只;1只提升主油缸、一套安全阀块及2只压力传感器、1只位移传感器、3只接线盒、62只锚具等部件。
3 设计要点分析
3.1 电液比例技术在钢绞线同步提升装置的应用
在3种同步加高装置中,控制主油缸伸缩的元件各不相同。
链板式液压同步提升加高装置采用开关阀来实现主油缸的伸缩,由2个开关阀实现快速伸缸,通过关闭其中1个开关阀实现慢速伸缸,其同步控制的策略是在各油缸位置之间的最大偏差值达到设定值(10mm)后将最快的油缸改为慢速运行以缩小偏差。缩缸通过1个开关阀来实现,其同步控制的策略是在各油缸位置之间的最大偏差值达到设定值后停止最快的油缸的收缩运行以缩小偏差。在伸缸的同步控制中,由于这套系统只有固定的快速、慢速两档速度来调节,同步效果受负载情况影响较大。在负载较为均衡的条件下,同步效果没有问题。如果负载相差较大,同步效果就差。在实际的岸桥提升应用中,如果4个门腿的重量偏差较大,经常会出现最轻的门腿和最重的门腿间的位移偏差越来越大无法缩小的情况,最后导致偏差>报警值(20mm)而停止自动运行。此时需将自动运行切换到手动模式运行,手动控制单个门腿的上升,在缩小门腿的偏差值到满足自动运行条件后再切换到自动运行。
多顶升料块式液压同步顶升加高装置,其主油缸油泵的转速是可以控制的,通过PLC程序对变频器发出指令,调节油泵的转速来控制油泵的流量进而控制油缸的位移速度,以此来控制各油缸行程的同步。每一个岸桥的门腿都配置了一个变频器和油泵马达,通过PLC传输速度指令,分为快速和慢速控制液压马达,调节液压流量。在同步顶升或同步下降的过程中,任意一个门腿的位置偏差>10mm时,系统会给偏差量大的门腿的油泵马达以减速命令,且位置偏差的判断在程序控制中保持实时性,当位置偏差>20mm时系统会即刻停止,需人工干预操作单个门腿,从而保证岸桥倾斜保证在安全范围内。这套系统除了4门腿的油泵马达需保持变频调速同步外,还要每个门腿顶升的两个油缸保持同步,而由于结构本身的原因,这两根油缸依靠结构刚性保证同步,但仍会有些偏差,因此在程序控制方面需选出左、右油缸的优先权,从而保证8根油缸的同步性。由于每个油泵马达是2个油缸的动力源,而这套系统控制的是油泵马达的流量,相当于控制的是2个油缸的平均速度,而参考的控制信号是单个油缸的位移,在控制量和被控量关系上不完全一致,要在程序中根据实际同步效果加入补偿。由于每个门腿的2个油缸之间的同步不可控,需要靠结构刚性来保持,这是这套系统在同步控制方面的另一个不足。
钢绞线液压同步提升装置是采用电液比例复合阀(流量和方向复合控制)来控制油缸伸缩的快慢和正反运动。电液比例复合阀的输入是4~20mA模拟量电信号,输出是反向到正向运动的0%~100%阀门开度,对应于油缸的缩运动和伸运动的0%~100%速度。电液比例阀是介于电液伺服阀与传统开关阀之间的一类阀,相对于传统的开关阀,它能通过改变信号的大小,方便实现无极调速且其控制精度比开关阀高,结构却更简单。而相对于电液伺服阀,其价格低、节能、维护方便,因而在现代工业领域得到了广泛的应用。由于在岸桥加高的实际应用中同步提升不需要太高的精度,只需保持同步偏差<10mm即可,因此油缸不需要连续的无极调速控制,同步伸和缩的控制策略和链板式液压同步提升加高装置类似:但由于比例阀自身具有无极调速的优点,因此这套装置的快速、慢速的速度设定可根据实际需要设定,实际应用中偏差控制非常迅速、同步效果好、适用性好,只采用相同的一套快、慢速参数即可适用于不同的桥吊加高项目,在整个加高过程实现了完全的自动同步提升运行。
以上3个加高装置中,采用比例复合阀的钢绞线同步提升控制系统在同步控制效果上最优,系统的电气、液压元件综合成本适中,系统适应性高、操控方便简单,推荐采用其作为实施同步控制的执行元件。
3.2 同步控制的实施关键:偏差比较
这套钢绞线液压同步提升装置有4组液压站共8个油缸,在上升、下降运行的同步控制中,在各个油缸位置之间的最大偏差值达10mm时,将上升、下降最快的油缸的运行速度从快速变为慢速,从而将最大偏差值控制在10mm内,达到各缸的同步运行。
偏差比较程序:8个油缸的位置在程序中分别以“A组油缸1位置”“A组油缸2位置”“B组油缸1位置”“B组油缸2位置”“C组油缸1位置”“C组油缸2位置”“D组油缸1位置”“D组油缸2位置”8个变量表示。
程序先给“油缸最大位置”变量赋值为0,然后“A组油缸1位置”和“A组油缸2位置”比较,将二者中的大值赋给“油缸最大位置”,接着“B组油缸1位置”和“油缸最大位置”比较,将二者中的大值赋给“油缸最大位置”,继续顺序比较“B组油缸2位置”……“D组油缸2位置”,得出所有8个油缸的“油缸最大位置”,然后各个油缸的位置和“油缸最大位置”比较,相等的就是最大位置的油缸。
类似地,先将“A组油缸1位置”赋值给“油缸最小位置”变量,然后“A组油缸2位置”和“油缸最小位置”比较,将二者中的小值赋给“油缸最小位置”,接着顺序比较完成8个油缸,得出所有8个油缸的“油缸最小位置”,然后各个油缸的位置和“油缸最小位置”比较,相等的就是最小位置的油缸。然后“油缸最大位置”减去“油缸最小位置”的值,就是8个油缸的最大偏差值。当此偏差值≥10mm时将最快的油缸控制为慢速运行。在上升工况中最快的油缸是位置最大的油缸,在下降工况中最快的油缸是位置最小的油缸。
3.3 系统的安全性
锚具的安全性:钢绞线液压同步加高装置的提升主要是通过上下锚具负载力的切换,结合主油缸的伸缩运动来提升或下降负载。无论何时上锚具或下锚具都必须有一个锚具咬合住钢绞线来承受负载的力量,否则负载就会坠落造成安全事故。锚具在设计上考虑了安全性,锚具由3个锚片组合成圆锥形状,上大下小,安装在一个圆锥形的槽内。在控制锚具松或紧的电磁阀都没有得电的状态,锚具在弹簧的压力下和钢绞线有一定的接触,如果钢绞线向下运动,锚具会由于和钢绞线的摩擦而自动咬合住钢绞线,从而锁住负载、防止坠落。
控制程序的安全性:上、下锚具同时松或紧的限制。在提升过程中上下锚具不能同时松,否则负载会坠落。如果采用自动运行,由于自动运行程序中没有出现上下锚具同时松的命令,因此自动运行在程序上是比较安全的。而在手动操作中,人为来控制上、下锚具的松和紧,如果控制人员不熟悉工况或误操作,就有可能发出上、下锚具同时松的命令,负载就会坠落造成事故。据悉,国内某著名厂家的控制程序中,手动操作工况里对上、下锚具的松、紧操作没有限制。完成加高过程后在下放承载梁时,出现过上下锚具同时松的误操作,导致承载梁坠落的事故。而在做加高的准备工作时,在地面将钢绞线穿入锚具的过程中,需要将油缸的上、下锚具同时打开,因此程序上不能直接限制上、下锚具同时松。
本套装置的程序做了如下设计:在手动操作时,如果操作人员同时发出上、下锚具松或紧的命令,系统不直接执行,而是弹出一个对话框给操作人员确认,操作人员输入密码确认后程序才执行命令,从而避免了误操作,增强了系统的安全性。
4 结语
通过介绍液压同步提升技术的特点和钢绞线液压同步提升技术在岸桥加高工程实际应用中的设计要点,给相关企业在类似的工程应用中设计钢绞线液压同步提升装置提供了有价值的经验和设计思路。
作者简介:曾毅(1971-),男,广西贺州人,上海振华重工(集团)股份有限公司高级工程师,研究方向:港口集装箱起重机电气方面的设计和改造。
参考文献
[1]卞永明.大型构件液压同步提升技术[M].上海:上海科学技术出版社,2015.
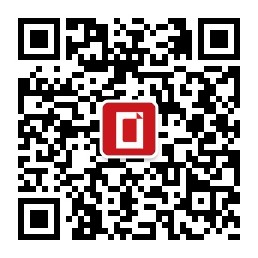