机械加工工艺技术误差分析及对装配质量的影响研究
- 来源:科技研究 smarty:if $article.tag?>
- 关键字:机械加工,工艺技术误差,装配质量 smarty:/if?>
- 发布时间:2021-06-30 19:36
摘要:我国经济时代的发展推动科学技术产品标准,而机械加工工艺技术方面,如何控制作业误差,提高装配质量,成为从业人员需要解决的重点问题。本文简单分析了几种常见的机械加工工艺技术误差,就如何减少机械加工工艺误差,提高装配质量进行了探讨,提出优化机械加工性能和措施的建议,推动机械加工行业可持续化发展。
引言
改革开放以来,我国科学技术正向着国际化水平发展,但就机械加工工艺技术方面,还存在着一定误差。许多机械生产任务是由生产线与机床夹具结合完成,但每个生产线与机床夹具的形状、颜色、体积等方面都存在着一定的差距,相应的加工技术要求也不尽相同。在机械加工环节,若采用相同的工艺制作方案,将会产生技术误差,影响机械装配质量。
1.常见机械加工工艺技术误差
机械加工工艺技术需要从组织结构及管理体系两个角度出发,重点包括机械设计与工程项目设计两方面,其中机械设计工作要求形成符合设计指标要求的设计方案,这个环节是要与订单需求相关并依次进行工作,而工程项目设计需要将设计方案转变为实际产品,即设计内容主要与机械产品制造有关。机械加工过程中,常会由于各种原因造成技术误差,严重影响项目装配质量,常见的技术误差包括以下几点:
其一,工具误差,常见的机械加工过程中,经常会用到刀具、扳手等工具,这些工具在长时间使用过程中会出现较大程度的磨损情况,使得机械加工环节出现几何误差,影响机械加工精准度,以及工艺品装配质量。
其二,定位误差,机械部件加工生产装配环节,尤其是对于钻模夹具这种精密度较高的机械任务中,若部件定位精准度发生偏移,导致机械出现计划外的故障,将会造成定位误差。这种误差是目前机械加工环节最为常见的问题,对于机械加工水平及成品质量有着决定性因素。
其三,工作人员误差,作为整个机械加工环节的操作人员,若其工艺技术不标准,将会造成严重后果。例如,转向架装配环节钳工需要根据侧架摆放的不同位置,将侧架放置到钳子顶尖上,并借助钳子顶尖进行整个侧架的移动、调整工作。钳工需要进行侧架承载支撑面与钳案平面之间的距离并进行记录,过程中尽量保证侧架的支撑面能够与钳工钳案之间处于平行状态,且侧架的导框能够与钳工钳案呈90 度放置。若由于工作人员个人操作疏忽导致偏离角不为90 度,将会无法获得准确的还原孔中心线,影响机械装配质量[1]。
2.减少机械加工工艺误差,提高装配质量方法探讨
2.1 优化机械加工设计
机械加工环节有些误差是可以避免的,与同类机械进行对比,通过预防的方式降低加工误差的可能性。以钻模夹具为例,进行钻模夹具装配作业环节,可以整合所有同类钻模夹具数值数据后,构建相应的参数数据库,在进行钻模夹具机械加工时,进行整个参数加工的横向比对,通过分析同一项目的数值变动情况,为钻模夹具机械装配工作设计提供合理变更意见,降低工艺误差产生的可能性。还可以通过参考钻模夹具已有的机型资料及成熟加工方案,并借此减少机械加工工艺误差,能够对钻模夹具加工环节的参数进行分析,重新估量机械设计方案数值,以及钻模夹具自身的成本评估。在机械加工设计环节,可以邀请专业机构对机械加工设计效果进行评估,将数据收集结果进行有效性分析,提高机械加工设计安全质量。将这些理想准机数值与实际情况进行对比,在多次调整后,获得钻模夹具机械加工的最优解,切实提高钻模夹具装配质量。
2.2 及时进行误差补救
机械产品进行装配生产加工过程中,难免会出现机械工艺误差,若及时进行误差补救,能够将损失降到最低,保证机械装配的有效性。例如,钻模夹具机床装配制造环节,长时间的作业使得加工环境温度升高,出现一定程度的加工误差。而滚珠丝杠可以将机械加工环节产生的拉伸力进行适应性调整,从而缩短机床的螺距,起到误差补救的效果,保证装配施工质量。此外,为保证机械装配加工工艺的有效实施,要定期进行加工数据核查,一旦发现机械误差要及时补救。
2.3 革新机械加工工艺
采用优秀的机械加工工艺,完善装配前期准备,能够有效避免机械加工误差。例如,进行钻模夹具薄片切割加工环节,常规加工方法是利用切割机直接进行作业,这种加工方法对设备损耗较大,且降低产品刚度。若在其加工环节使用环氧树脂,以增强薄片零部件的光滑性,再在磁力吸盘上进行固定打磨,能够有效降低对于加工设备的磨损程度,且薄片自身强度不会受到过大影响。实际加工环节,要选择合理的加工方案,革新机械加工工艺,降低机械加工环节的误差影响,保证机械产品装配质量。
2.4 重视加工工艺检测
机械加工完成后,需要对加工结果进行专业化检测,在进行装配作业,尤其对于钻模夹具这种精密度、信息集成度较高的机械设备,更要进行细致化的误差分析,保证装配作业质量。重视数字化体系构建,不能只考虑制造工具的数字化应用,而要将加工误差检测作为核心指导思想,借助数字化发展实现机械加工技术创新。传统机械检测环节会对完成品造成一定损伤,现代机械加工误差检测环节,主要使用电磁信息进行参数检测。数据采集装置为机械加工工艺检测的核心部分,在机械内部探测信号经由传感器到达数据采集装置后,在ARM-Cortex M0 内核的LPC1768 芯片帮助下,进行以太网数据处理。将其扩展到外部存储FLASH 设备,使得前端传感器信号经过滤波处理,在采集装置中进行A/D 信号转换,并以脉冲编码器的形式进行信号输出,利用CPU 进行信号采用。经过对数据信息的实时处理,分析出机械加工的误差情况、误差原因等内容,确定误差位置,并将所有检测信息录入中心计算机系统。为保证机械加工工艺误差的分析准确性,可以使用KEIL MDK 开发平台,对整个装配机械进行系统化分析。采用模块化信号设计系统,在提高处理器资源有效使用的同时,提高整个数据采集传输报警系统的功能性[2]。
结语
科技的进步推动我国机械事业发展,机械加工工艺技术误差分析及装配质量控制,对于机械运行的安全性及稳定性有着直接影响作用,相关作业标准较为严格。在工业技术高速发展背景下,通过减少机械加工技术存在的误差,采用合理有效的解决措施,降低误差影响,从而提高机械加工工艺产品的质量和技术。
参考文献:
[1]梁艳丰.机械加工工艺技术误差分析及对装配质量的影响[J].湖北农机化,2020(17):122-123.
[2]管西强.论机械加工工艺技术产生的误差及优化控制策略[J].世界有色金属,2019(22):239+241.
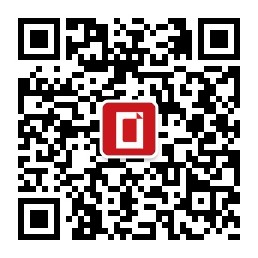