增材制造:更快的打印,更低的成本
- 来源:国际塑料商情 smarty:if $article.tag?>
- 关键字:复合,材料,行业 smarty:/if?>
- 发布时间:2022-04-17 17:51
复合材料行业一直将增材制造(AM)视为一种生产原型和小批量复合材料零件的更快、成本更低的方法。然而,这种看法正在发生着变化,随着行业不断探索新技术,价格上更具竞争力的3D零件能够实现大规模生。
AM技术和营销顾问里克•内夫(Rick Neff)表示,业界对AM的兴趣日益浓厚,有部分原因是台式和中型工业3D打印机已经越来越实用。有多家公司对这些打印机进行应用上的实验和拓展,他们通常将碳纤维、玻璃纤维甚至芳纶纤维与热塑性塑料或光固化聚合物结合在一起。
与此同时,大规模增材制造(LSAM)技术也取得了进步。例如,Thermwood Corporation就建立在橡树岭国家实验室(ORNL)及其合作伙伴开发的大面积增材制造(BAAM)机器的基本概念之上。Thermwood的LSAM机器使用连续冷却过程,以确保每一打印层都能够处于理想的温度。LSAM增材制造系统目前已经能够生产出适合众多行业应用、几乎完美融合的大型热塑性复合材料结构,
2014年,BAAM最大的打印部件为6英尺长、20英尺宽、8英尺高;而如今Thermwood的1540 LSAM机器可以以更快的速度生产40英尺长、15英尺宽、5英尺高的零件。这为航空航天和船舶制造商快速生产大型工具带来了新的机遇。
“当我们考虑开发原型飞机时,成本和交货周期的很大一部分归因于生产过程。如果你不得不需要几个月的时间来获得部件,那么你就一定需要至少几个月来建造一架飞机。但如果你能在一两周内获得这些部件,将彻底改变飞机原型制作的整个过程。”
Neff还指出,材料供应商已经开发了一系列专门为AM设计的产品。通过添加碳纤维或玻璃纤维,将热膨胀系数降低10倍或一个数量级。“当你打印零件时,不会收缩太多,也不会有零件变形和改变形状的情况发生。”他说。
建筑应用
Neff认为,增材制造的进步,尤其是大规模增材制造(LSAM),将为建筑市场提供新的机遇。虽然围绕3D打印建筑混凝土有很多炒作,但真正的创新以及更好的经济主张,在于打印用于浇注混凝土的复合材料形式。
作为艺术品或是博物馆的展品——建筑师们发现了使用3D打印复合材料创造独特形状的潜力。一个例子是拉斯维加斯突袭者队体育场的阿尔•戴维斯纪念火炬,它由225个复合材料块制成,这些块由碳纤维增强的聚碳酸酯复合材料3D打印而成。
建筑师普拉特•博伊德(Platt Boyd)创立了Branch Technology公司,因为他对传统施工方法和材料的限制感到失望。受到自然形式和结构的启发,Boyd找到了一种将这些元素融入建筑中的方法,利用机器人、自由形式的3D打印使设计自由成为可能。
Branch Technology的项目开发经理David Goodloe说:“我们有一个专有的挤压机制和专有的算法,可以引导机器人通过路径。实际上,这种材料在挤压过程中会在自由空间中凝固,这让我们能够进行打印,就好像机器人是一支巨大的钢笔,在空气中绘制三维路径,并在其尾迹中留下一种增强聚合物。”
其结果是体积晶格结构的强度与可比较的固体形式相似,但使用的材料却少了20倍。如果结构的一个区域需要额外的强度,可以改变蜂窝单元的尺寸以增加该位置的结构密度。Branch Technology使用一系列材料,包括带有短切碳纤维和各种添加剂的粒状热塑性聚合物树脂。
尽管该机器人可以打印30英尺长、10英尺宽、12英尺高的零件,但大多数零件的尺寸在15×8×8英尺(约合1.83米)左右。Goodloe指出,复合材料部件的尺寸通常受到物流瓶颈的限制,比如门洞大小或卡车装载,而不是打印技术。
Branch Technology公司拥有三种产品。
Branch Matrix™是聚合物树脂和纤维添加剂的外露晶格结构。“它适用于建筑和雕塑应用——大而宽的几何形状。”Goodloe举例说,芝加哥菲尔德自然历史博物馆中心大厅的四个巨型空中花园Nature Clouds就是由该公司打印的。
BranchClad™是一种大规模定制的通风雨幕系统和附着在建筑物结构上的建筑表皮。它采用格子结构与防火、节能的填充泡沫制成,可以构建独特的外观。目前,该公司正在为阿拉巴马州的美国太空和火箭中心进行覆层工作,后者准备复制月球的拓扑结构。
StoPanel®3DP是公司通过与建筑构件预制商合作推出的,它为建筑商提供了在外部和内部都完全完工的墙体组件。
增材制造中的乐高模式
用于无人机的3D打印电机支架的呈现爆炸式增长,促使Orbital Composites公司的创始人兼首席技术官科尔•尼尔森(Cole Nielsen)开始重新思考增材制造。首先,他花了18个月的时间研究了目前使用的每一种制造方法,特别强调了先进复合材料和顺序工艺兼容性。
Nielsen开发了一种新型打印头,即同轴挤出机。喷嘴中又内含喷嘴,它将细丝(例如连续碳或玻璃纤维或铜线)包裹在热塑性或热固性树脂管内。该技术允许在打印过程中包含多种材料。
Nielsen还发明了一种高强度、高压力的长丝驱动装置,可以令打印速度更快的同时减少长丝故障。
Orbital Composites公司不使用带有龙门架的传统3D打印机。相反,该系统采用单机器人和多机器人设置,较小的机器人堆叠在较大的机器人之上。其不同的末端执行器执行特定的任务,例如打印和预处理或后处理。机器人可以在重叠的运动领域中协同工作,从而加快生产速度。它们可以轻松打印弯曲的形状,并且与使用龙门架的3D打印系统不同,这些机器人可以制造九倍于自身尺寸的产品。如果一个机器人在制造过程中发生故障,另一个机器人可以代替它,打印过程不会中断。该公司围绕其生产的产品设计每台打印机的设置。Nielsen将其比作将不同的乐高积木组合在一起以达到所需的形状。
虽然这个硬件很重要,但这只是故事的一部分。“我们50%甚至更多的工程工作是软件上的。我们一直试图弄清楚机器人如何移动才能完成打印——实际上你可以尝试多种不同的方式来穿过迷宫。”他解释道。
经济实惠的大批量生产
尽管Orbital Composites公司能够打印卫星零件或天线等高科技产品,但其首批客户之一却是Lore,该公司为自行车手提供定制打印的碳纤维鞋。Lore声称,其每双售价1,900美元的鞋子将优化骑手的功率输出和踩踏效率。
顾客使用iPhone应用程序扫描自己的脚并将测量结果发送给公司,该公司使用Orbital Composites的技术打印鞋子。Lore同时强调其产品的可持续性。他们的鞋子由可回收的热塑性塑料制成,打印过程几乎没有任何的浪费。
“这双鞋证明了Orbital Composites可以使用12轴、先进的热塑性塑料、连续纤维经济高效地制造打印产品。”Nielsen说。利用这项技术,该公司计划很快制造和销售自己的无人机系列。
Orbital Composites目前正在与能源部、ORNL和缅因大学合作开展一个项目,以3D打印技术生产含有连续纤维的风力涡轮机叶片。目标是证明现场打印风力叶片的可行性。
ORNL的另一个项目涉及增材制造压缩成型(AMCM)的开发。Orbital Composites首席执行官Amolak Badesha说:“这台特殊的机器旨在以汽车价格和生产率生产具有航空航天质量的热塑性连续纤维和部件,具有汽车生产的可靠性和A级表面光洁度,且没有材料的浪费,因为AMCM系统可以打印零件的净重和净形状。”Badesha表示,注塑成型会产生10%的浪费,压缩成型会产生20%的浪费,而钣金冲压会产生55%的浪费。
热固性AM的进展
自2013年成立以来,Massivit 3D一直专注于通过大规模3D打印实现更快、更具成本效益的制造。它的打印系统是独一无二的,使用基于热固性光敏树脂的打印凝胶。
“大多数复合材料的增材制造工具系统都依赖于利用热塑性材料的分层机制,这种分层过程会导致在构建过程中形成不均匀的分子键。”全球销售和营销副总裁Ido Eylon说。据该公司称,将于5月上市的Massivit 10000将第一个各向同性3D打印模具引入复合材料制造领域。利用专有的热固性铸造材料,该技术可在高温下保持一致的低热膨胀,以及高达155 C的高热稳定性。
Massivit 10000采用了动态铸造技术,并在CAMX 2021上获得了卓越复合材料奖。打印头使用一种快速的紫外线固化聚合物来形成两个外部牺牲壁,每个壁厚约3.6毫米。浇注头随后在这两个壁之间沉积环氧基树脂复合材料,形成各向同性芯。
打印机逐层构建模具,直到达到所需的尺寸和形状。最大尺寸为56英寸宽、59英寸高和44英寸深。硬化后的打印部件可在高温下后固化数小时,以改善机械性能,然后浸入水中,外壁会剥落。(水中的碎屑可以去除,水可以重复使用。)从水中出来的模具接近净形。模具表面可能需要后处理。
该过程将模具生产通常需要的19个步骤减少到仅4个,因此使用Massivit 3D打印机的公司将在不到一周而不是几周内获得模具。
一些项目已在Massivit 10000上打印,包括用于赛车座椅的复杂模具。但还有许多其他潜在的应用。“各种工具和心轴都可以数字化生产,用于运输、家居装修、体育和航空航天行业。”Eylon说。
随着增材制造技术的成熟,公司将继续寻找新的、更好的方法来单独使用3D打印或与其他复合材料制造技术结合使用。结果应该是更快、更好和更具成本效益的生产方法,这将为复合材料行业在许多市场中提供竞争优势。
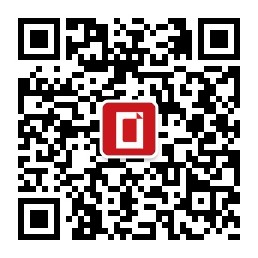