304不锈钢管热强旋成形试验研究
- 来源:不锈钢商圈 smarty:if $article.tag?>
- 关键字:不锈钢,润滑剂,热强旋 smarty:/if?>
- 发布时间:2015-07-20 13:49
摘要:针对304不锈钢常温下加工硬化严重、塑性变形抗力大的特性,对304不锈钢筒形件进行了热强旋成形试验研究以探索304不锈钢的热强旋成形规律。在HGQX-LS立式热强旋旋压机上,以二硫化钼为润滑剂,采用高频电磁感应加热方式进行3道次、总减薄率为60%的旋压成形试验。试验主要分析了成形温度和进给比对成形质量的影响,试验结果表明,热强旋是成形304不锈钢薄壁筒形件行之有效的方法之一,当温度为1000℃、进给比为0.4mm·r-1时能得到成形质量良好的旋压件。
关键词:304不锈钢;热强旋;成形质量;成形温度;进给比
旋压是借助于旋轮的进给运动,加压于随芯模沿同一轴线旋转的金属毛坯,使其产生连续的局部塑性变形而成为所需空心零件的一种近净精密塑性成形方法,具有材料利用率高、工具简单、成形精度高、可提高力学性能等优点。目前,304不锈钢薄壁筒形件主要采用多道次冷旋+中间退火的方法成形,但该方法工序繁多、成形效率低、且因中间退火须多次装夹而导致旋压件成形精度较差。热成形是将工件加热到再结晶温度以上进行的塑性成形,与冷成形相比,热成形具有变形抗力小、塑性好、成形极限高、降低对设备动力和刚度要求的特点,是成形难变形金属最有效的途径之一。本文对304不锈钢筒形件热强旋成形工艺进行分析,重点分析了成形温度、进给比对成形质量的影响,用以获得合适的热强旋成形方法及工艺参数。
1 热强旋成形试验
1.1试验材料及装备
试验材料为304不锈钢管,管坯内径Φ50mm、壁厚5mm(图1),旋后工件壁厚要求为(2±0.2mm);室温下的力学性能如表1所示。
双锥面旋轮结构简单、容易制造,适用于中等厚度(一般为2~8mm)筒形毛坯,试验中旋压毛坯壁厚为5mm,采用双锥面旋轮,旋轮型面参数如表2所示;由于所用毛坯为管坯,因此采用反旋方式进行旋压成形。传统的热强旋成形大多采用火焰喷枪在旋压过程中对坯料进行加热,或者旋前在加热炉中将坯料加热至所需温度,旋压过程中不进行补热。前者加热温度难于控制;后者随着旋压成形过程的进行,坯料温度逐渐下降,对热加工温度范围窄的材料不适用。因此,提出采用加热速度快、温度分布均匀的高频感应加热方式进行加热(图2),同时通过红外线测温仪对成形区温度进行监测、结合温控仪对高频感应加热设备输出功率进行调节,以实现坯料温度的实时反馈控制、控温准确,控制流程如图3所示。
试验在HGQX-LS立式热强旋旋压机床上进行,图4展示了正在进行中的304不锈钢热强旋成形试验。热强旋成形过程中,旋轮外表面与坯料之间的摩擦不利于旋压成形过程中金属的流动,常常会导致旋压件表面质量差、甚至出现表面起皮等成形缺陷。因此,在每道次旋压前采用耐高温润滑剂二硫化钼水剂对管坯外表面进行润滑,可以有效地改善了其成形质量。
1.2试验工艺参数设计
对钛、钼等难变形金属进行热强旋时,道次减薄率在30%以下能得到成形质量较好的旋压件。本文热强旋总减薄率为60%,因此试验中采用3道次热强旋成形,各道次减薄率如表3所示。加热温度的高低对材料强度和塑性有重要影响,是热强旋成形最主要的工艺参数之一。温度过高时材料强度大大降低,易产生堆积隆起,温度过低则达不到改善材料塑性的目的。进给比的大小不仅影响旋压件的成形质量、导致堆积隆起等旋压缺陷的产生,还会直接影响到生产效率,故对热强旋成形温度和进给比进行试验研究。
304不锈钢的敏化温度区间为500~850℃,在该温度区间成形时会沿晶界析出铬的碳化物,造成晶界铬的含量降低,导致耐腐蚀性下降,易发生晶间腐蚀;而在900~1050℃高温退火时,合金组织会发生再结晶,退火软化效果明显,故在该温度区间进行不同温度下的热强旋成形。
由于热态下材料的塑性好,为防止旋压时产生堆积和隆起等旋压缺陷,应选取较小的进给比进行成形。热强旋过程中,存在坯料与芯模及旋轮的接触传热、坯料与周围环境的对流散热、坯料在高温下自身的热辐射散热等多种形式的散热。为防止因芯模与坯料之间的温差过大而导致坯料与芯模之间的接触传热严重,进而使坯料内外表面温差过大,产生表面裂纹等旋压缺陷,在热强旋前对芯模进行适当的预热,预热温度为600℃。这样既有利于减少坯料和芯模之间的传热,也不会因为预热温度过高而显著降低芯模的强度。
2 热强旋试验结果分析
2.1加热温度对旋压件成形质量的影响
为研究旋压温度对热强旋工艺的影响,获得合适的热强旋温度,在进给比为0.4mm·r-1、加热温度分别为900,950,1000和1050℃时进行热强旋工艺试验,所获旋压件如图5所示。利用超声波测厚仪和百分表等测量工具分别对不同温度条件下旋压件的壁厚偏差、直线度和椭圆度进行测量,沿工件圆周方向每隔90°、轴向每隔10mm测量一组数据,测量点位置如图6所示,测量结果如表4所示。由图5可见,在4种温度条件下,管坯热强旋成形均能顺利进行,表面质量良好。这是因为304不锈钢在900℃以上发生了动态回复和动态再结晶,材料的塑性得到了较大提高。由表4可见,加热温度为900~1050℃时,旋压件的壁厚偏差、直线度和椭圆度较小,壁厚分布较均匀。但随着变形温度的升高,动态再结晶进行得越来越充分、强度逐渐下降,在950℃以上变形抗力明显小于950℃以下的变形抗力,对旋压设备吨位要求低,同时考虑到当加热温度为1050℃时,将因加热温度较高,坯料通过热传递散失给芯模的热量多、坯料内外层的温差大导致成形精度降低,因此,1000℃是304不锈钢热强旋成形较合适的旋压温度。
2.2进给比对旋压件成形质量的影响
为进一步研究进给比对304不锈钢热强旋成形过程的影响,在加热温度为1000℃时,分别以进给比0.2,0.4,0.6和0.8mm·r-1进行试验,所获旋压件如图7所示。由图可见:当进给比为0.2,0.4和0.6mm·r-1时,热强旋成形能顺利成形;但当进给比为0.8mm·r-1时,随着旋压过程的进行,旋轮前方的材料出现了隆起和堆积。这是由于随着进给比的增大,变形金属来不及向旋轮后方流动、使得旋轮前方的材料形成堆积和隆起。
表5为加热温度为1000℃时、不同进给比下旋压件的壁厚偏差、直线度和椭圆度的影响。由表可见:工件整体壁厚分布在1.995~2.182mm之间,最大壁厚偏差为0.159mm;进给比由0.2mm·r-1增加到0.6mm·r-1时,工件的直线度和椭圆度略有减小,同时,壁厚分布较均匀;但当进给比为0.4mm·r-1时,工件的壁厚偏差最小。这是由于在一定范围内进给比越大,工件的贴模性越好,而贴模情况的好坏直接影响工件的成形质量;贴模情况越好成形质量越高,但是当进给比增大到一定程度时,单位时间内参与变形的金属材料增多,材料变形的不均匀性增大,导致壁厚偏差有增大趋势,甚至产生变形失稳。
由表4、表5还可以发现,旋后工件壁厚值几乎都大于2mm、较理论计算值偏大。这是由于旋压过程中材料的热胀冷缩、机床的退让以及旋后材料的回弹三者共同作用的结果。
3 结论
(1)针对常温下塑性变形抗力大、加工硬化严重的304不锈钢管,采用高频加热方式进行强旋成形是一种行之有效的方法。可避免传统火焰喷枪加热时温度难以控制及加热炉加热时随着旋压成形过程的进行,坯料温度逐渐下降导致旋压过程不能顺利进行等缺陷。
(2)合适的加热温度及进给比是热强
旋过程顺利进行的重要保证。对304不锈钢管而言,当加热温度为1000℃、进给比为0.4mm·r-1时,旋压件的壁厚偏差、直线度和椭圆度较小,壁厚分布较均匀,可获得较好的成形精度。
文/杜军 夏琴香 朱宁远 谢红希
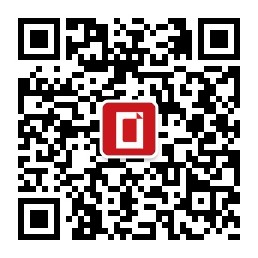