水泥生产全流程智能制造模式
- 来源:国企管理 smarty:if $article.tag?>
- 关键字:水泥生产,智能制造,转型升级 smarty:/if?>
- 发布时间:2024-05-17 21:15
创造单位:安徽海螺集团有限责任公司
主 创 人:任 勇 何承发
创 造 人:李群峰 李乐意 李晓波 詹家干
[摘 要]运用人工智能和信息网络等新一代信息技术与水泥制造技术融合,推动水泥工业生产、管理和营销模式的变革,已成为我国水泥行业高质量转型发展的关键。海螺集团聚焦生产管控、设备管理、安全环保和营销物流等核心业务,按照工业互联网相关标准,以数字工厂建设为目标,建成了行业首个包含智能生产、智能运维和智慧管理三大平台的水泥生产全流程智能化工厂,并迅速推广应用,初步形成了“以智能生产为核心、以运行维护作保障、以智慧管理促经营”的水泥生产全流程智能制造模式,为传统产业的转型升级和高质量发展发挥了标杆引领作用。
[关键词]水泥生产;智能制造;转型升级
一、实施背景
目前,水泥行业正处于转型升级的关键时期,企业信息化、自动化和智能化水平参差不齐,亟需采用融合工艺机理的信息化、智能化技术,推动生产、管理和营销模式从局部、粗放向全流程、精细化和绿色低碳发展方向变革,以解决资源、能源与环境的约束问题,提高生产制造水平和效能,实现水泥行业“降成本、补短板”和跨越式发展。
运用人工智能和信息网络等新一代信息技术与水泥制造技术融合,推动水泥工业生产、管理和营销模式的变革,已成为我国水泥行业高质量转型发展的关键。
安徽海螺集团有限责任公司(简称“海螺集团”)作为水泥行业龙头企业,在水泥生产过程管控方面有着深厚的工业积淀,不仅拥有水泥工艺、电气自动化、机械装备和工业信息化等专业技术人才队伍,而且建立了专业化的信息技术工程公司。
30多年来,海螺集团对水泥自动控制、装备管理、工艺操作和供应链管理进行不断地总结和优化,并通过计算机应用软件进行固化和统一,形成了具有海螺特色的水泥生产知识库,促进了水泥产业的高标准化和集团高速发展,也为集团水泥智能工厂建设奠定了良好基础。
近年来,海螺集团以企业实际需求为导向,针对原料来源多、质量波动大、质量检测及时性准确性不足、生产操作依赖人工经验、产品发运环节劳动强度大等问题,深入分析行业生产管理现状,通过聚焦生产管控、设备管理、安全环保和营销物流等核心业务,按照工业互联网相关标准,以数字工厂建设为目标,建成了行业首个水泥生产全流程智能化工厂,并快速推广应用,初步形成了集团水泥智能工厂集群。(见图1)
二、主要做法
海螺集团采用自主研发与集成创新相结合的方式,以典型生产线为试点,由点到面逐步推广应用,并运用5G+AI等最新技术持续迭代升级,不断提升智能工厂技术及应用水平。
水泥智能工厂包含智能生产、智能运维和智慧管理三大平台,具体包括数字化矿山管理系统、专家自动操作系统和智能质量控制系统等八个涵盖水泥生产全过程的智能化控制及管理系统。
(一)基于智能生产平台,实现“一键输入、全程智控”生产
智能生产平台包括数字化矿山管理系统、专家自动操作系统和智能质量控制系统。该平台在行业率先构建了“一键输入、全程智控”的生产模式。只需在智能质量控制系统中输入熟料或水泥的质量预控目标,系统自动根据原燃材料信息完成生产配料,并向数字化矿山管理系统下达开采和配矿指令。专家自动操作系统按照配料参数和品质要求在节能稳产模式下自动引导生产。进入智能生产闭环后,开采的矿石品位和终端产品的质量数据则又会由系统自动实时采集分析,用以不断优化生产方案,使产品品质、能源消耗等控制目标不断逼近预设的最优参数,最终实现降低人员劳动强度、提高产品生产品质和降低资源能源消耗的运营目标。
1.数字化矿山管理系统
该系统涵盖了矿山三维建模、中长期采矿计划、爆破、取样化验、采矿日计划、精细化配矿、GPS车辆调度、矿车无人驾驶、卡车装载量监量、混矿品位在线分析、配矿自动调整、生产管理、司机考核等矿山管理的各领域,实现了三维采矿的智能设计、配矿质量在线分析、矿车调度优化管理、矿山生产立体化管控,解决了水泥企业在矿山生产方面存在的配矿、监督和管理问题,提高了矿山生产效率、资源利用率和安全保障。
2.智能质量控制系统
进厂原煤、入堆场石灰石等大宗原燃材料采用在线式跨带中子活化分析仪进行实时检测,并建立堆场质量数据三维模型;生料、熟料、水泥等经全自动取样器取样,由炮弹输送系统送至中央实验室,通过机械手、粉磨压片一体机等全自动制样设备进行制样,并由中子活化在线分析、激光粒度仪、X荧光分析仪及XRD衍射仪等检测分析设备进行自动检测。
结合海螺多年来的生产控制经验,还开发了自动配料软件系统,形成了集自动采样、样品传输、在线检验、自动化验和智能配料一体化的管理平台,实现了对原料、燃料、熟料和水泥等各类物料的全程自动取样、化验分析和配料调控。(见图2)
3.专家自动操作系统
该系统利用世界先进的实时智能专家系统开发平台,针对水泥生产过程中长滞后、多变量、难检测和多扰动的特点,将大数据分析、人工智能技术与海螺工匠实操经验完美结合,建立海螺集团水泥生产知识库,搭建最符合水泥生产的专家自动操作系统。
专家自动操作系统以MPC(模型预测控制)、规则控制、模糊逻辑控制等先进的控制理论为基础,将海螺集团水泥工艺控制思想进行标准化、软件化,并与DCS控制系统、数字化矿山管理系统和智能质量控制系统无缝集成、协调共进,实现水泥生产线的智能化操作控制,摆脱人为操作的波动性,使生产线始终以最佳参数自动完成熟料、水泥的连续稳定生产。(见图3)
(二)基于智能运维平台,实现能耗精细化管理、设备预测性维护
智能运维平台主要为智能生产平台提供高效、安全、节能、环保的运行环境,包括设备管理及辅助巡检、能源管理和安全环保管理三大系统,具有“稳产助优产、优产促节能、节能优环保”的特点。
1.设备管理及辅助巡检系统
该系统利用现代化网络和通信技术,通过温度压力传感器、振动检测器、高清视频摄像仪和移动巡检等先进仪器,实现对原料立磨减速机、回转窑主电机、高温风机等设备运行、保养、检修和故障诊断的管理,并通过PC端与手机App数据交互,达到“降低劳动强度、信息实时共享、提高管理效率”的目标。
同时,将重大设备故障自检测、主要设备实时在线监测、点巡检移动物联网化、三维仿真全息管理四大功能全面融合,实现设备在线监管、重大故障提前预判。
2.能源管理系统
水泥行业是能源消耗大户,能源消耗占水泥生产总成本的50%以上,节能减排对水泥行业可持续发展具有重要意义。
能源管理系统,通过对水泥生产过程的用煤、用电、用油等能源消耗数据进行在线收集、实时传输,并结合各工序产量、设备开停状态等生产过程数据,对各工序电耗进行统计、分析,对吨石灰石、吨熟料、吨水泥能耗进行对标分析,以及对能源指标数据的横向比较等,有效提升水泥工厂能源管理水平,从而使水泥企业的能源管理由传统方式、常规方式向可视化、数字化、网络化、智能化转变,达到节约用煤、减少用电的效果。
3.安全环保管理系统。按照原国家安监总局下发的《企业安全生产标准化基本规范》和《冶金等工贸行业企业安全生产预警系统技术标准(试行)》等规定要求,海螺集团以“集团、二级子公司、三级子公司”为架构,以“四大要素、八大指标”为纲要,开发了安全环保管理系统。系统从企业领导决策者、安全环保管理者、安全环保参与者等多维度出发,围绕“事前、事中、事后”三条业务主线,通过信息化技术手段,帮助企业建立“日常监管、提前预警、事中救援、事后提高”的涵盖安全环保管理全过程的业务系统。
(三)基于智慧管理平台,实现企业经营决策数字化
智慧管理平台包含生产制造执行系统和营销物流管理系统,在系统整合智能生产和智能运维平台数据的基础上,推动工厂的卓越运营。
1.制造执行系统
水泥制造是典型的流程化生产。在生产过程中,各工序的生产调度、生产部门间的组织协调、销售部门的发运组织、各职能部门的职能管理,乃至企业级的整体运营决策等行为,都需要及时、有效的数据支撑。
通过制造执行系统的实施,构建以产品生产为主线,贯穿生产调度、物资、能源、设备、质量、安全环保、统计等环节的生产全过程管理平台,打通智能工厂各系统间数据壁垒,实现各大工业智能系统的互联互通、全面融合,支撑生产管理业务全面信息化,提高生产效率,降低生产成本,使得企业始终以最优化、最经济的方式生产。
2.营销物流管理系统
传统的水泥工厂都设有销售大厅,车辆排队签单、开票,工作既耗时又繁琐。
通过“互联网+物联网”技术的应用,构建包含水泥电商平台、物流通道无人值守、水泥全自动包装、产品流向监控子系统的营销物流管理系统,将互联网销售、工厂智能发运和水泥运输在线监管全面融合,实现工厂订单处理、产品发运、货物流向监控等业务流程无人化和数据应用智能化,提升服务质量与效率、互动参与度以及便捷性,为客户提供更为方便、快捷的服务,实现水泥传统营销、管理模式的创新和升级。
三、实施成效
(一)经济效益
海螺集团水泥智能工厂充分融合了生产工艺特征和集团多年在生产过程管控方面深厚的工业积淀,实现了数据的大平台、大交换、大融合,真正做到了生产工序操作全自动、过程分析全数据的智能化生产。
以2条标准的5000t/d生产线进行智能工厂综合效能考核评测,系统运行效果如下:
数字化矿山管理系统通过对矿体三维地质建模、采剥编制、计算机优化,集成在线质量分析与检测等设备,实现了自动化配矿和车辆智能调度,每年可多搭配低品位矿石34万吨,柴油消耗同比下降3%,轮胎消耗同比下降36%。
专家自动操作系统通过“小幅多频”自动优化控制代替人工操作,使原料磨、回转窑、煤磨、水泥磨、余热发电机组等水泥生产主机设备始终逼近最佳状态运行,实现熟料产量提升6.6%,标准煤耗下降5.58kg/t,操作员劳动强度降低90%,综合在线达到98%以上,产品稳定性显著提升。
智能质量控制系统投运后,入堆石灰石CaO堆平均合格率提升7.22%,熟料f-CaO合格率提升3.52%,熟料28天强度上升1.10MPa。取消矿山化验及部分过程样品的人工取、制、检工作,大幅降低了取样人员劳动强度和安全风险。
设备管理及辅助巡检系统投入运行以后,水泥烧成系统机电设备故障率下降70%,备件消耗下降20%,现场巡检工作量下降40%,设备运行周期延长37%,专业用工优化20%以上。
海螺集团水泥智能工厂建成实施后,主要经济技术指标得到持续优化,员工劳动强度得到有效减轻,取得了良好的经济效益。生产线设备自动化控制率达100%、劳动生产率提升30.89%、资源综合利用率提升5%,能源消耗下降5.2%,质量稳定性提升3.7%;各类资源消耗下降及劳动生产率提升带来的经济效益每年达7650.95万元。预计,水泥智能工厂在集团全面推广完成后,各类资源消耗及劳动生产率提升带来的经济效益每年逾10亿元,对水泥等传统行业具有较好的借鉴意义。
(二)社会效益
海螺集团水泥智能工厂建设,在水泥行业首次实现了全流程智能化技术应用,通过装备智能化、生产管控智能化和商业智能化的深度融合,促进了水泥行业发展的信息化和智能化,推动了水泥企业生产方式的变革,对我国水泥行业转型升级和高质量发展具有重要意义。
通过建设由数字化矿山管理系统、专家优化控制系统以及智能质量管理系统组成的智能生产平台,实现了水泥生产全过程的三维地质建模、采剥编制、计算机优化、小频多幅自动调整、在线质量分析与检测等智能制造模式和方法,有效提升了能源资源的综合利用率。以全椒海螺为例,系统投运后每年可多搭配低品位石灰石34万吨,节约标准煤耗2.24万吨。若在全国推广落地后,预计每年可多搭配低品位石灰石1.29亿吨,节约标准煤849万吨。
智能化管控技术的应用减少了水泥生产过程中的温室气体排放,增强了对工业废弃物的处理能力。以全椒海螺工厂为例进行测算,系统投运后每年可减排二氧化碳2.95万吨,多消纳煤矸石、粉煤灰、脱硫石膏等工业废渣16万吨;若在全国推广落地后,预计每年可减排二氧化碳1118万吨、多消纳工业废渣6000万吨,有力地促进了水泥行业向绿色制造迈进。
四、思考探讨
随着新技术、新装备的应用,水泥行业迈向智能化已势在必行。未来的水泥企业集团将会由单一生产水泥、熟料的制造型工厂,升级为涵盖上下游产品的多业态水泥产业集群,对资源综合利用率、生产效率和成本管控方面的要求将进一步提高。
从整个水泥行业来看,智能制造目前仍处于起步阶段,下一步应继续以水泥生产实际需求和痛点问题为导向,加强技术研发和集成创新,在自动寻优、跨系统协同、机器人应用、5G及AI等方面持续开展智能制造系统迭代升级,并借鉴离散型行业智能制造技术及经验,扩大智能制造应用范围,提升水泥工业智能制造技术水平,持续保持行业领先地位。
水泥智能工厂是建立在工厂稳定运行基础上更高层次的提升和优化。在实施智能工厂建设之前,应持续加大工艺、装备及信息系统等方面的投入,进一步提升物料输送、设备监控、DCS系统、基础网络等方面的稳定性和可靠性,为智能工厂的稳定高效运行提供基础条件。
在现有的水泥智能工厂体系基础上,结合人工智能、大数据、5G+AI等新一代信息技术的前沿科研成果,开展水泥智能工厂迭代升级、工业互联网平台搭建等技术的攻关研发,提高水泥行业整体智能化水平,推动传统制造向数字制造、智能制造转型升级。
高度重视水泥工厂智能化核心技术和基础软件平台的开发,进一步加强对自主知识产权工业基础软件和智能装备的研发和支持力度,切实解决部分底层基础软件平台和智能装备系统的“卡脖子”问题,对全面提升我国水泥工业智能制造自主化水平有重大现实意义。
总的来看,水泥智能制造技术本质上是IT(信息技术)和OT(运行技术)技术的融合,应用的关键就是要立足于企业的实际需求,利用最新和最适用的信息技术赋能企业的生产和管理,提升企业生产和管理效益。
作为水泥生产企业在开展智能制造系统建设时,不能完全依赖系统解决方案供应商或者照搬照抄其他企业方案,必须要从自身的实际需求出发,并全程参与其中,切实解决影响智能制造系统运行的设备、流程和管理问题,才能充分发挥出智能制造系统的作用。
编辑/王盈 统筹/李斐
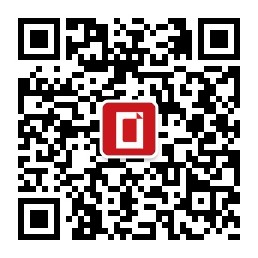