高性能节约型不锈钢制备技术研发与应用
- 来源:不锈钢商圈 smarty:if $article.tag?>
- 关键字:高性能,节约型,不锈钢,技术 smarty:/if?>
- 发布时间:2014-11-13 12:34
摘要:开发了409L和410S铁素体不锈钢冷轧板的淬火-配分(Q&P)工艺,获得了铁素体、马氏体和残余奥氏体的复相组织。通过优化奥氏化温度、淬火温度和配分时间,获得了尽量多的马氏体和残余奥氏体。与常规退火和淬火-回火(Q&T)工艺相比,Q&P工艺获得了最优的强度和延伸率组合、连续性屈服和适中的n值、r值,达到了高强度和易成型的要求,能够替代先进高强钢用于生产汽车结构件。
关键词:不锈钢;淬火;配分;高强度;易成型
1、前言
2012年我国汽车产量超过1.9×107辆高居世界首位,成为拉动经济发展的重要产业,这也对钢铁产业产生了重要影响。2012年汽车用镀锌板用量约为6.0×106t,锌消耗量约为3.0×105t。但是,我国锌资源的储量和保证年限远低于世界平均水平;而且,我国报废汽车的镀锌板再冶炼时,产生的锌尘绝大部分被排入大气,即使在发达国家,也有多于20%的锌尘被排入大气。因此,锌资源的过度消耗及其造成的环境破坏是汽车产业可持续发展所面临的严峻考验。
目前,这一问题受到全球汽车产业的高度关注,发达国家的汽车制造开始大量使用高性能不锈钢。这是因为:不锈钢板的耐蚀性远优于镀锌板;而且,实际使用中,镀锌板一旦表面锌层局部破损,其使用寿命将锐减,尤其是车辆下部和发动机盖等经常受水气侵蚀的部位;更重要的是,不锈钢板再冶炼时可以完全被回收。在德国和意大利等欧洲国家,经过20多年试验,目前80%的大型客车使用全不锈钢构件。以全生命周期计算,全不锈钢客车的成本比普通客车低约20%,可100%回收,且避免了表面涂镀和锌尘污染等对资源与环境造成的负担。因此,用不锈钢板取代镀锌板,既能使汽车用钢长寿命化,又能使汽车产业可持续发展。
然而,含镍的300系奥氏体不锈钢成本过高,同样受到稀缺性镍资源的严重制约。因此,汽车结构用钢应发展基本不含镍的节约型不锈钢。此类不锈钢中,最常用的是400系铁素体不锈钢,其具有良好的塑性,且材料成本与热镀锌普碳钢基本相当,但强度偏低,故应用于厨房用具、家用电器和汽车排气系统等领域。因此,要将其应用于汽车结构件领域,又要满足汽车用钢轻量化的发展要求,必须改进传统400系铁素体不锈钢的显微组织结构,制造出强度和塑性均较好的节约型不锈钢。
2、高强度易成型钢板制备理论基础
相变强化是提高钢板强度和塑性的常用手段。最初工艺是将高温奥氏体淬火至马氏体相变结束温度(Mf)以下再回火,使其转变为回火马氏体的淬火-回火(Q&T)工艺。回火马氏体强度高,虽然韧性尚可,但塑性差。后来,开发出将高温奥氏体淬火至贝氏体相变开始温度(Bs)与结束温度(Bf)之间,保温一段时间再淬火至室温,使其转变为回火贝氏体和残余奥氏体的贝氏体区回火工艺。残余奥氏体的相变诱发塑性(TRIP)效应使此种组织塑性好,但回火贝氏体的强化效果不显著。近年来,Speer等提出了综合前两种工艺优点的淬火-配分(Q&P)工艺,其将高温奥氏体淬火至马氏体相变开始温度(Ms)与结束温度(Mf)之间,再升温至稍高于Ms进行保温,最后淬火至室温,使其转变为回火马氏体和残余奥氏体来提高强度和塑性。Q&P工艺起初用于普碳钢,最近拓展至不锈钢。给出了铁素体不锈钢经Q&P工艺处理时的热历程和组织演变:由于较高的Cr含量和较低的C、N含量使其高温无单一奥氏体区,故加热至Ac1温度以上的(奥氏体+铁素体)两相区;然后淬火至Ms~Mf,高温奥氏体部分相变为马氏体,部分未相变;再加热至比Ms稍高的温度,马氏体发生回火,同时,马氏体及铁素体内过饱和的固溶C、N原子向未相变奥氏体内扩散,使之由于固溶C、N的富集而更加稳定;最后淬火至室温,被C、N充分稳定的奥氏体可保留至室温,稳定不充分的奥氏体仍相变为马氏体。
与普碳钢相比,不锈钢Q&P工艺的优势在于:高于12%的Cr含量使其淬透性较强,在淬火过程中会促进马氏体相变,抑制铁素体、珠光体和贝氏体相变,在配分过程中又抑制未相变奥氏体发生贝氏体相变,这些均有利于最终马氏体和残余奥氏体的获得。因此,本文研究了利用Q&P工艺制备高强度、易成形的节约型不锈钢板,使之应用于汽车结构件领域。
3、高强度易成型不锈钢板制备技术研发
实验选用0.9mm厚的409L和410S不锈钢冷轧板。实验优化后的Q&P工艺是将两个钢种的冷轧板用加热炉分别加热至1030℃和1000℃保温3min,再分别淬火于350℃和240℃盐浴中,然后均放入400℃盐浴中配分15min,最后均水淬至室温,制成了Q&P处理板。作为对比:将409L和410S上述工艺中的350℃和240℃盐浴均换为室温水淬,其余工艺不变,制成了Q&T处理板;另外,将409L和410S冷轧板分别加热至930℃、退火4min和800℃、退火1h,再空冷至室温,制成了常规退火板。
由于高温奥氏体是提高强度和塑性的马氏体和残余奥氏体的来源,为此需要确定两个钢种的奥氏体化温度。将409L和410S冷轧板试样均加热至800~1200℃的多个温度保温5min,再水淬至室温,用光学显微镜观察组织,将其中的马氏体对应于高温奥氏体,以此确定两者高温奥氏体含量随温度的变化。由于两个钢种Cr含量均较高、且C、N含量较低,因此,两者高温均无单一奥氏体区,仅有(奥氏体+铁素体)两相区。409L的两相区存在于950~1180℃,高温奥氏体含量在1030℃达到极大值37%;410S的两相区存在于840~1200℃,高温奥氏体含量在1000℃达到极大值73%。与409L相比,410S较多的C、N含量使其高温奥氏体的存在温度区间更宽、峰值含量更多。为了挖掘两个钢种提高强度和塑性的最大潜能,两者均以高温奥氏体含量极大的温度为奥氏体化温度。
由于淬火温度应设定为Ms~Mf之间的合适温度,为此需要确定两个钢种的马氏体相变温度。将409L和410S的Φ3mm×10mm圆柱形试样放入相变仪中,分别加热至1030℃和1000℃保温5min,再均以50℃/s的冷速冷却至室温。示出了冷却过程中,马氏体相变区间试样的长度变化曲线。用切线法处理曲线,可知:409L的Ms为400℃、Mf为300℃;410S的Ms为330℃、Mf为150℃。与409L相比,410S较多的C、N含量使其马氏体相变发生较为滞后、持续时间较长。通过曲线的偏移量可知,410S的相变马氏体量约是409L的两倍。
由于Q&P后,大部分高温奥氏体相变为马氏体,仅小部分残留至室温,而残余奥氏体具有TRIP效应,是成品在强度提高的同时又保持塑性的关键。因此,在奥氏体化程度一定的前提下,获得尽量多残余奥氏体是Q&P工艺的目标。相关研究发现:淬火温度和配分时间均影响残余奥氏体的含量。为此,应用X射线衍射(XRD)仪对不同Q&P工艺参数处理后的样品进行了检测,并通过衍射峰强度计算了残余奥氏体含量。
409L与410S冷轧板经过优选的Q&P工艺处理后XRD衍射谱线,为方便比较两者,410S的谱线向上平移了250个强度单位。在两者谱线中,首先检测出强度较高的铁素体和马氏体的{110}、{200}、{211}、{220}和{310}晶面衍射峰,由于铁素体、马氏体的晶格参数十分接近,故两者同名晶面衍射峰基本重合;其次,检测出强度较低的残余奥氏体的{111}、{200}、{220}和{311}晶面衍射峰。与409L相比,410S较多的高温奥氏体使其残余奥氏体的衍射峰强度较高。
由XRD检测的409L由1030℃淬火至300~400℃和410S由1000℃淬火至150~330℃,然后两者均于400℃配分900s后,淬火温度对残余奥氏体含量的影响。当淬火温度在(Ms+Mf)/2附近时,残余奥氏体含量最多;当淬火温度由此值向Ms或Mf变动时,残余奥氏体含量均逐渐减少。这是由于:当淬火温度靠近Ms时,淬火至Ms~Mf后未相变奥氏体较多,配分后含量有限的固溶C、N使奥氏体内固溶C、N浓度整体较低,这样的奥氏体在淬火至室温时易转变为马氏体,最终残余奥氏体含量较低;当淬火温度靠近Mf时,淬火至Ms~Mf后未相变奥氏体较少,虽然配分后奥氏体内固溶C、N浓度较高,容易在淬火至室温后保留下来,但最终残余奥氏体含量较低。因此,优选的淬火温度为(Ms+Mf)/2。
由XRD检测的409L由1030℃淬火至350℃和410S由1000℃淬火至240℃,然后两者于400℃配分10~6000s后,配分时间对残余奥氏体含量的影响。当配分时间增加至约900s时,残余奥氏体含量逐渐增加;当配分时间继续增加时,残余奥氏体含量又逐渐减少。这是由于:当配分时间<900s时,随时间延长,C、N向未相变奥氏体内的富集进行得愈加充分;当配分时间>900s时,随时间延长,马氏体内碳化物的析出会增加,C、N向未相变奥氏体内的富集会逆向进行,同时未相变奥氏体分解为贝氏体+碳化物也会加剧。因此,当配分温度为400℃时,优选的配分时间为900s。
两个钢种的冷轧板分别经过优化的Q&P和常规退火处理后的扫描电子显微镜(SEM)照片。经Q&P处理后,两个钢种内均可见板条状马氏体和平整的铁素体,但无法识别马氏体内残余奥氏体。409L含有稳定化元素Ti,其析出物种类较多,包括:分布位置对铁素体、马氏体无选择性的边长约5μm的立方体TiN(标记为A)和边长约500nm近方体Ti(CN),标记为B,以及分布于马氏体内轴径约30nm、长约250nm的针状(Fe,Cr)3C(标记为C)。410S不含稳定化元素,其析出物仅有分布于马氏体内轴径约50nm、长约500nm的针状(Fe,Cr)3C。
经常规退火后,两个钢种均为铁素体基体。409L内析出物有:与经Q&P处理后特征相似的TiN和Ti(CN),以及直径40~80nm的球状TiC(标记为D)和(Cr,Fe)23C6(标记为E)。410S内析出物仅有0.4~1μm的球状(Cr,Fe)23C6。由于常规退火和其后空冷在(Cr,Fe)23C6和TiC的主要析出温度区间540℃~Ac1,停留时间较长,因此其析出物总量明显多于经Q&P处理后。
两个钢种的冷轧板经过优化的Q&P工艺处理后透射电子显微镜(TEM)照片。明场像中大块区域为一高温奥氏体晶粒内的马氏体,其具有板条亚结构和高密度位错,周围的铁素体晶粒位错密度较低。暗场像是由残余奥氏体的特征衍射光获取的。来自于同一高温奥氏体晶粒的残余奥氏体具有基本一致的晶体学取向,其主要以薄片状分布于马氏体板条之间和以多边形分布于高温奥氏体晶界处。410S的薄片状残余奥氏体宽50~300nm,较409L的50~100nm宽大,且总量较多。
4、性能评价
按国标(GB/T228.1—2010)的要求,沿轧向截取拉伸试样,进行拉伸实验。图9示出了两个钢种的冷轧板分别经过优化的Q&P、Q&T和常规退火处理后拉伸试样的工程应力-应变曲线。与常规退火和Q&T工艺相比,Q&P工艺获得了最优的强度和延伸率组合,这得益于马氏体的强化和残余奥氏体的TRIP效应;而且,其屈服平台完全消失,这是由于屈服平台产生于拉伸变形初期,铁素体内位错的扩展和增殖受到固溶C、N原子形成的柯氏气团钉扎,而Q&P工艺的奥氏体化和配分过程使固溶C、N原子向马氏体和残余奥氏体内富集,最终,铁素体内固溶C、N原子显著减少,柯氏气团效应消失,而且在二次加工中,工件表面也不会出现影响外观的吕德斯带;另外,此工艺还获得了较为适中的加工硬化指数n值和塑性应变比r值,这保证了二次加工的潜能。与409L相比,410S较高的C、N含量使其各相应工艺的强度较高,延伸率、n值和rQ&P和常规退火处理后,电化学腐蚀实验的极化曲线。Q&P后的点蚀电位为0.14V,高于常规退火后的0.10V,即Q&P后点蚀的发生要滞后于常规退火后。这是由于:常规退火后,富Cr的(Cr,Fe)23C6析出较多,这造成其周围基体贫Cr,耐蚀性降低;而Q&P后,虽有(Cr,Fe)3C析出,但其总量较少、且富Cr程度较低。
5、结语
本文研究了利用Q&P工艺制备高强度、易成型的节约型不锈钢板。
1)选用409L和410S冷轧板,于高温奥氏体含量最多的温度进行奥氏体化,再淬火于Ms~Mf,又配分于稍高于Ms的400℃。当淬火温度为(Ms+Mf)/2、配分时间为900s时,最终可获得较多的残余奥氏体。
2)Q&P工艺获得了铁素体、马氏体和残余奥氏体的复相组织。409L内析出物有分布位置对铁素体、马氏体无选择性的TiN和Ti(CN)以及马氏体内的(Fe,Cr)3C;410S内析出物仅有马氏体内的(Fe,Cr)3C。残余奥氏体分布于马氏体板条之间和高温奥氏体晶界处;与409L相比,410S的残余奥氏体较宽大、总量较多。
3)与常规退火和Q&T工艺相比,Q&P工艺获得了最优的强度和延伸率组合、连续性屈服和适中的n值、r值,达到了高强度、易成型的要求。与409L相比,410S强度较高,延伸率、n值和r值稍低。
4)采用Q&P工艺制备409L,获得了较常规退火工艺更高的点蚀电位,提高了其耐蚀性。
文/谢胜涛 刘振宇 王国栋
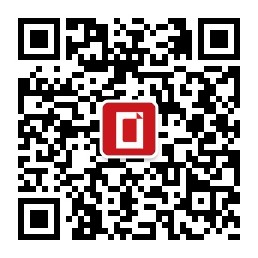