O,N和Ni含量对0Cr25Ni7Mo4N双相不锈钢热轧塑性的影响
- 来源:不锈钢商圈 smarty:if $article.tag?>
- 关键字:oCr25Ni7Mo4N双相不锈钢,相比例,氧化物夹杂 smarty:/if?>
- 发布时间:2014-11-13 12:57
摘要:对不同o,N和Ni含量的oCr25Ni7Mo4N双相不锈钢进行了1200℃,4道次热轧实验。利用oM,SEM和EBSD观察分析了实验钢的组织和夹杂物。结果表明,低o,N和Ni含量的实验钢热轧塑性良好。o含量为0.0059%的实验钢中夹杂物主要为Al2O3和Mgo·Al2O3,分布于晶粒内部,未对热塑性造成不良影响。o含量为0.038%和0.046%的实验钢则发生了轧制边裂,开裂处为α/γ相界,相界内的大颗粒Cr2O3和MnO2夹杂是造成开裂的主要原因。其中o含量较低(0.038%)的实验钢,由于N和Ni含量过高,使钢中γ相体积分数在热轧状态时高达60%。过多的γ相降低了γ晶粒内部的总应变量,使其不足以发生再结晶软化,最终造成更严重的热轧开裂。
关键词:oCr25Ni7Mo4N双相不锈钢,相比例,氧化物夹杂,热塑性
双相不锈钢是指固溶组织中铁素体(α相)与奥氏体(γ相)含量各约占一半的一类不锈钢。双相不锈钢同时具备高强度、高韧性以及良好的耐点蚀、耐应力腐蚀性能,已经成为石油化工、海洋工程领域的重要钢铁材料。但是由于其热塑性差、热轧容易开裂,因此生产难度非常大。针对双相不锈钢热变形微观机理、热塑性影响因素的研究,一直是国内外的热点课题。
在早期的研究结果中,大多认为由于γ和α两相的强硬度不同,造成应力分布不均、热塑性差。而近年来,国内外大多数学者认为是由于两相在高温下的动态软化机制不同,即γ相为动态再结晶、α相为动态回复的机制,α相先于γ相软化,从而造成了双相不锈钢变形不均匀和开裂。因此,普遍认为通过提高变形温度、减少其中某一相的比例至10%以下,甚至获得单相组织,是改善热塑性的重要手段。另外也有文献指出,细化晶粒有助于改善双相不锈钢热塑性,如姜忠良等研究表明,经过750℃,38h的σ化处理(即δ铁素体共析分解反应δ→γ+σ),获得了非常细小的α晶粒,使得双相不锈钢的塑韧性大幅度提高。
本工作针对相同热加工工艺下,同一种双相不锈钢的热塑性不同的现象,拟从窄成分范围控制角度,研究O,N和Ni含量与γ/α两相比例、显微组织和夹杂物种类数量之间的关系,并分析通过控制O,N和Ni含量对提高双相不锈钢热塑性的作用。
1 实验方法
按照SAF2507超级双相不锈钢的标准成分要求,对O,N和Ni含量微调,冶炼制得3种0Cr25Ni7Mo4N超级双相不锈钢试样。其中,No.1钢为AOD炉冶炼并经过Al和硅铁还原后浇铸制得,No.2和No.3为纯金属原料经真空感应炉熔炼后浇铸制得。
将实验钢切成80mm×40mm×20mm的热轧坯,随炉升温加热至1200℃并保温1h,在350热轧板带机上经4道次轧成5mm厚钢板,总压下量75%,道次压下率分别为20%,30%,30%和30%。终轧温度980℃,轧后立即水淬。
分别截取实验钢的铸态、轧前(即铸态经1200℃,1h固溶水淬处理)和轧后试样,经机械研磨、抛光和电解侵蚀后利用DM2500光学显微镜(OM)观察试样显微组织形貌。电解液为10%草酸(C2H2O4)溶液,电压为7V,时间25s。
采用FeritscopeFMP30仪测量试样的α含量,每个试样不同部位测10次并取平均值。通过ULTRA55热场发射扫描电镜(SEM)及能谱仪(EDS)观察裂纹和夹杂物形貌、分析化学成分。利用显微硬度仪和电子背散射衍射仪(EBSD)进行了实验钢中γ和α两相的硬度及热轧板侧面应变分布的研究。
2 实验结果与讨论
2.1 实验钢的热轧塑性
3个实验钢在1200℃经4道次热轧后的宏观形貌。由图可见,实验钢表现出不同的热塑性。No.1钢坯在整个轧制过程中表面保持完好,没有产生裂纹;No.2和No.3钢坯则均在第1道次时即有边部裂纹产生,在随后的轧制过程中,裂纹逐步加深,最终形成严重的边部开裂。
由于3个实验钢所采用的热轧工艺相同,所不同的仅是合金元素含量,其中,容易引起热塑性恶化的C,P和S含量,在No.2和No.3钢中与No.1钢中相当或更低,因此C,P和S含量不是造成No.2和No.3实验钢热塑性差的主要原因。本工作将重点讨论O,N和Ni的含量对0Cr25Ni7Mo4N双相不锈钢热塑性的影响。
2.2 N含量及γ/α相比例变化
目前国内外对于双相不锈钢γ/α相比例对其热塑性的影响。研究认为,当γ或α某一相的数量超过20%~25%时,钢的热塑性急剧降低,热变形将出现裂纹等缺陷,当两相比例各为50%时热塑性最差。因此对于SAF2101和SAF2205等低牌号双相不锈钢,一直采用较高温度下的α单相区热加工的工艺制度。
0Cr25Ni7Mo4N双相不锈钢由于合金元素含量高,高温下也难以进入单相区。列出了实验钢在铸态、轧前、轧后各阶段的α相含量。No.1钢α相含量在各阶段均最高,轧制前相比例γ/α=50.98%﹕49.02%;No.3钢中α相含量略有降低,γ/α=54.61%﹕45.39%;No.2钢的α相含量最低,轧前两相比例γ/α=63.77%:36.23%,这跟No.2钢中的奥氏体稳定化元素Ni和N含量高有关。另外,实验钢在不同工艺阶段的α相含量也不同,这与各阶段处理方式不同有关。根据文献,SAF2507钢在900~1300℃区间,随温度降低α相减少、γ相增加。实验钢铸坯是凝固后在较快冷却速率下获得的,相比例受冷却过程中发生的相变影响;轧前状态为高温急冷获得,相比例接近高温状态;终轧温度低于开轧温度,轧后α相数量减少。
轧制前3个实验钢的相比例都没有接近单相区,也就是说,都没有达到可以获得良好塑性的相比例区间。其中No.1钢轧前γ/α相比例接近50%:50%,处于热塑性最差区域,然而其热轧表面完好。相反,No.2钢的轧前γ含量为63.77%,处于热塑性略好的相比例范围,但是实验中其热轧开裂却最严重。因此可以推断,相比例并不是影响双相不锈钢热塑性的关键因素。
2.3 金相显微组织
0Cr25Ni7Mo4N实验钢在铸态和轧前态的金相组织照片。铸态组织中,灰色为α相,白亮色为γ相。可以看出,No.1钢为粗大的树枝晶形貌,同时伴有魏氏组织;No.3钢组织的整体形貌与No.1钢接近,即柱状树枝晶和魏氏组织共存,但晶粒比No.1钢细小。No.2钢的晶粒组织则为棒状或岛状γ浮在α基体上,没有出现魏氏组织。这是因为其Ni和N含量高,组织中γ相稳定,在冷却过程中不易发生相转变。对比2.1节所述3个实验钢热轧开裂情况,可以看出,铸造组织的晶粒形貌和尺寸不是影响0Cr25Ni7Mo4N双相不锈钢热塑性的主要原因。
经1200℃,1h固溶淬火处理后的试样,显示了实验钢在轧制前的组织,如图3d~f所示。从中可见,α相上出现了密集的弥散分布的黑色细小颗粒状析出物。这是因为高温下α相中N的固溶度大,室温时固溶度大幅度下降,而由于水冷时间较短,N原子来不及从α相扩散至周围的γ相中,因此在α相中的原始固溶位置上原位析出Cr2N颗粒,以降低α相中N的过饱和度。另外可以看出,No.2钢中析出的Cr2N较少,这是因为No.2钢中γ相体积分数高,可溶解大量N,因此α相中过饱和固溶的N比较少,急冷析出的Cr2N也就比较少。需要注意的是,这些Cr2N颗粒仅仅是在高温淬火急冷条件下才会析出,而在高温加热和轧制过程中是以Cr原子和N原子的形式固溶在α基体里。
从轧前组织来看,No.2钢为粗大的花瓣状或树枝状γ相分布在α基体上。No.1和No.3的形貌依然比较接近,为长棒状γ交叉分布在α基体上,且No.3钢的组织比No.1钢细小。然而从热轧塑性来看,No.1钢热轧塑性好,但是No.3钢却发生了边裂。因此可以看出,晶粒的细小和均匀性,没有成为影响双相不锈钢热塑性的关键因素。
2.4 O含量及夹杂物分析
3个实验钢OM像中都有一些黑色颗粒。由于经过1200℃,1h固溶处理后,依然不能溶解,因此可以推断出是高熔点的夹杂物.同时可以看出,No.2和No.3钢中的夹杂物含量明显多于No.1钢,尺寸也比No.1钢中的大。
夹杂物是影响不锈钢塑性的重要因素。
双相不锈钢内的夹杂物主要与P,S,O有关,由这些元素形成的夹杂物,在塑性加工时易在其周围造成应力集中点,从而降低不锈钢的塑性,进而影响钢材表面和边部的质量。对比实验钢的化学成分可以看出,实验钢的P和S含量相差不多,但No.2和No.3钢的O含量大大高于No.1钢,约为其7倍左右。这必然使得No.2和No.3钢的氧化物夹杂数量更多、尺寸更大。
经过高对比度处理后的SEM像,证实了此推论。每个试样选取10个不同的位置进行夹杂物大小和数量统计。可以看出,No.1,No.2和No.3钢中的夹杂物数量之比约为2:6:10,而平均尺寸之比约为4:11:11,即No.2和No.3钢中的夹杂物数量是No.1钢的3或5倍。同时,No.1钢中所有夹杂物的尺寸均<10μm,其中84.21%夹杂物尺寸<5μm。但是No.2和No.3中超过60%的夹杂物尺寸>10μm,其中大约10%的夹杂物甚至超过了15μm。
进一步通过SEM和EDS对实验钢的夹杂物进行了成分标定。为了更精确地分析化学成分,试样没有被侵蚀。No.1钢中夹杂物颗粒,呈等轴或近球状,颗粒尺寸3μm,经EDS标定为Al2O3和MgO·Al2O3,这一类夹杂物是Al脱氧后的产物,试样内部没有发现除此之外的Mn,Cr或Fe的氧化物。未脱氧的No.2和No.3钢内部的夹杂物形貌及化学成分,可以看出夹杂物尺寸均大于10μm(甚至20μm),形状不规则,经标定为MnO2和Cr2O3。在No.2和No.3钢中都观察到了这2种夹杂物。
SEM结果为夹杂物在实验钢中的位置。可以看出,No.1钢中的夹杂物大多处于晶粒内,而No.2和No.3钢中粗大的夹杂大多处于γ/α相界。金属塑性理论指出,处于相(晶)界的夹杂物、析出物会降低晶粒间界面的结合能力,对金属塑性不利。
从上述观察可以看出,热轧塑性好的No.1钢与热塑性差的No.2和No.3钢之间的主要区别是氧化物夹杂的数量、大小、种类和分布。
进一步对No.2和No.3钢热轧板边部的裂纹进行了观察和分析,No.2钢裂纹处的SEM像和EDS分析结果。可以看出,轧制裂纹沿着α和γ相界产生,并且在裂纹处有大量10μm左右的夹杂物颗粒,其大小形貌与变形前相同。根据EDS分析结果可以看出夹杂物为Cr2O3。可见晶界(相界)处的大颗粒氧化物夹杂是造成实验钢热轧开裂的主要原因。
2.5 N和Ni含量及应变不均匀性
双相不锈钢热变形时软化机制不同,α相是通过动态回复,即亚晶内的位错滑移;而γ相则是当应变高于临界值时的动态再结晶。因此热轧时应变首先发生在先软化的α相内,然后逐步转移至γ相再诱发其再结晶软化。由于软化机制和顺序不同,热加工时容易造成γ和α两相中应力和应变分布不均匀,导致相界形成裂纹并扩展。文献报道,γ和α两相强度比值σγ/σα与应变分布εγ/εα有直接关联,当σγ/σα接近1时,两相中的应变分布也趋于均匀,将有利于改善钢的热塑性。因此,提高硬相γ相强度的元素(如N),对热塑性不利。
本工作中,No.2钢比No.3钢的O含量低、杂质少,但热轧开裂更为严重。对比分析其成分发现,No.2钢中的Ni和N含量明显高于No.3钢。N作为固溶强化元素,可极大地提高γ相的强度和硬度。但是本工作中的实际测量结果表明,无论铸态还是轧前固溶态,3个实验钢中的γ相的显微硬度没有差别,具体数值见表4。即No.2钢中较高的N含量没有使得γ相的σγ值升高,也没有提高γ和α两相强度比值σγ/σα。这主要因为Ni和N可以扩大γ相区、稳定γ相,从而使得No.2钢中γ相体积分数较高(表2),因此N在γ相中的实际浓度并没有提高,γ相的强硬度也没有提高。
通过EBSD对实验钢热轧板侧面进行了应变分布的研究。可以看出,No.1钢的变形非常均匀,轧后γ和α两相分层平行分布,没有发生不均匀的交叉扭曲等现象。该图右列为热轧板的变形状态分布图,是根据区域内各点取向差大小来判定晶体畸变程度以及所处的变形状态的。可以看出,No.1钢中γ和α两相均为黄色,即处于变形后回复状态,说明此时两相晶粒内部的畸变都很小。不过,在部分相界处存在红色的尚未回复也未再结晶的变形畸变区域。这表明,双相不锈钢变形时发生了相(晶)界滑动,由此造成的畸变在热变形过程中不易软化,并易造成应力集中。因此,如前文所述,如果在相(晶)界处存在氧化物夹杂则必然造成热塑性下降。
No.2和No.3钢的变形均匀性明显低于No.1钢。2个实验钢中的γ相都发生了不同程度的扭曲。从图中右列变形状态布图可以看出,No.2和No.3钢中的α相已基本软化,而γ相中仍存在大量未回复也未再结晶的畸变区,尤其晶粒形貌扭曲的γ相,其内部的晶体畸变非常严重。这说明这部分γ相的应变量还没有达到再结晶所需要的临界应变。
从显微硬度的检测结果可以看出,在轧制之前3个实验钢中,γ相的硬度是相同的。因此,造成No.2和No.3钢中γ相的变形不足,不能诱发再结晶的原因,不是其强度高引起的应变量不足,而是其体积分数过大,从而形成连片的粗大的γ晶粒,使得变形协调性下降、变形量不足,最终无法诱导再结晶软化。Ni和N含量越高,γ相体积分数越大,则γ相应变越不足,越难以发生再结晶软化。Ni和N含量高的No.2钢中红色畸变区域明显多于No.3钢。这种高的Ni和N含量造成的γ相应变不足,难于再结晶软化的现象,是造成0Cr25NiMo4N双相不锈钢热变形开裂的另一个主要原因。
3 结论
(1)经Al和硅铁脱氧后的0Cr25Ni7Mo4N双相不锈钢中,仅含有少量细小的Al2O3和MgO·Al2O3夹杂,分布于晶粒内部,未对热塑性造成不良影响.
(2)未经脱氧的实验钢,易在相界形成粗大的Cr2O3和MnO2夹杂,使得相界结合力下降。同时,双相不锈钢热轧过程中发生相界滑动,不易软化,易造成应力集中,使得热轧开裂。
(3)N和Ni含量增加虽然没有造成γ相的硬度升高,却使γ相体积分数增加,并形成成片的粗大的γ晶粒,因而造成γ相应变总量降低,不足以发生再结晶软化,降低了钢的热塑性。
(4)对于双相不锈钢,应控制N和Ni含量在SAF2507标准成分的下限,使得其在高温变形区时的γ体积分数不超过50%。
文/陈雨来 张泰然 王一德 李静媛
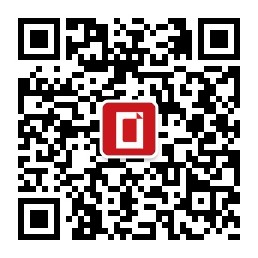