不锈钢薄板色差产生原因与消除方法探讨
- 来源:不锈钢商圈 smarty:if $article.tag?>
- 关键字:不锈钢薄板,色差,原因,消除方法 smarty:/if?>
- 发布时间:2014-11-13 12:43
摘要:介绍了不锈钢薄板轧制过程中轧制工艺参数和轧制油对板面质量的影响,分析了西南某不锈钢厂偏8辊轧机生产过程中板面出现色差的原因及解决办法,对比了两种轧制油的使用效果。新开发的轧制油轧制不锈钢薄板时不会出现色差等表面质量缺陷,而且轧制的带钢更薄,提高了生产效率,降低了生产成本。
关键词:不锈钢;薄板;轧制;轧制油;色差
引言
中国不锈钢生产始于1952年,起步较早,但发展缓慢,1980年,中国不锈钢板材产量仅为2万t,1988年达到11.8万t。20世纪90年代以后,随着人民生活水平的快速提高,不锈钢在厨房用具、建筑装饰材料等领域得到广泛应用。2001年,中国已成为世界不锈钢第一大消费国。在需求的推动下,国内不锈钢生产结束了30多年的徘徊,从1999年起快速发展,并开始走向专业化、规模化生产。
2011年我国不锈钢板热轧产量1270万t,冷轧产量950万t。今后一段时期不锈钢板冷轧产能还会有较大增长,2013年正在开工建设或准备建设的连轧生产线有太钢、宝钢德盛、福建福欣、广州联众、北海诚德、广东宏旺、吴航不锈钢等,单机架可逆轧机生产线有四川天成、宏旺集团等。从国际上看90%的不锈钢薄板都是用20辊森基米尔轧机的,在中国由于大量中小民营企业资金的限制近年上马了很多偏8辊轧机。装备水平良莠不齐、产品品种多样化,使得所用轧制油的质量也多种多样。
不锈钢板面微观粗糙度不同使其反光性能产生差异,在视觉效果上形成“色差”,色差是不锈钢薄板生产过程中常见的一种表面缺陷。引起色差的因素很多,原材料即热轧板厚度、硬度、金相组织差异可以引起色差,背衬轴承、中间辊表面缺陷可以引起色差,单道次压下率过大可以引起色差,轧制油流量不足、喷射不均匀、润滑性能不足也有可能导致色差的产生等。本文以西南某不锈钢厂生产实际情况讨论全油型不锈钢轧制油在偏8辊轧机轧制200系列不锈钢薄板时色差的产生原因和消除办法。
1、原用油情况
四川某不锈钢有限责任公司以西南不锈钢为依托,配备2条1450偏8辊冷轧机,1条连续酸洗退火线,还配备分条、开平、8K、钛金,对不锈钢表面进行深加工处理,生产不锈钢2B磨砂板、8K镜面板、黄钛板、玫瑰金板、黑钛金板,年加工冷轧卷材能力8万t,年加工不锈钢装修板材6万t。偏8辊轧机的主要技术参数如下:
原料材质:200系、300系;
钢带宽度:1000~1300mm;
原料厚度:≤3.0mm;
成品厚度:0.25~2.0mm;
轧制力:1200kN;
轧制速度:≤200m/min;
辊系规格:工作辊:(150~160)mm×1450mm。
该厂现有轧制工艺是1#机生产厚度大于0.63mm的产品,采用一个轧程,8道次;2#轧机生产厚度小于0.60mm以下的产品,采用两个轧程,8~10道次,中间退火一次。两台轧机使用同一种轧制油进行生产。
原用轧制油存在的缺陷:在1机上使用原来轧制油轧制200系列不锈钢时,只能生产0.7mm厚的成品,生产0.63mm的产品时带钢中部产生明显的色差。为提高产品表面质量,该厂希望在1#轧机上换用性能更好的轧制油。
2、新不锈钢轧制油应用
2.1 新不锈钢轧制油技术指标的确定
根据生产实际需要,要求轧制油要有充分的润滑性、钢带表面不能出现热划痕,满足现场轧制工艺要求;满足轧制品种多样化的要求;提高板形控制能力降低对来料板形的依赖性;最大限度地降低能耗及其他消耗。
2.2 新轧制油使用过程中出现的问题
制0.7mm厚产品时,轧制力较前有明显降低。并出现严重的中浪,后将工作辊凸度由0.25mm逐渐减少到0.22mm,消除了中间浪。轧制0.63mm厚产品时,在第三道次出现轻微的色差,在轧制第五道次后逐渐减少,最后一个道次后色差完全消失。为了生产表面质量更好的产品,杜绝生产过程板面色差,轧制油供应商和使用方分析了各种可能改进的因素并决定从以下几个方面入手解决现有问题。第一:调整轧制过程中前、后张力设定;第二:提高轧辊粗糙度;第三:调整轧制油喷射压力、流量、角度;第四:调整轧制油的润滑、极压抗磨性能。
2.2.1 前后张力调整对色差的影响
现场轧钢工程师曾有过调整前后张力消除色差的经验,通过现场前、后张力的调整并没有消除色差。
2.2.2 轧辊粗糙度对色差的影响
提高轧辊粗糙度也是消除色差的方法之一。其他工艺参数不变的情况下,将轧辊粗糙度由原来的0.3μm提高到0.5μm,结果表明:轧制0.63mm薄板时,对消除色差没有什么帮助。
2.2.3 轧制油喷射角度的影响
轧制油的主要作用就是润滑、冷却轧辊和带钢,轧制油喷射量不足、喷射不均匀会导致对轧辊、带钢的冷却不足、冷却不均匀,造成辊缝大小不一、润滑不均衡,从而导致局部压下量不同形成色差。但由于现场轧制油喷射系统中泵的流量已经开到最大,轧制油喷射压力、流量已经没法调整,只能调整喷嘴的角度以调整轧制油对轧辊的冷却能力。通过喷射角度的调整色差有所减轻,但还是不能完全消除色差。
2.2.4 提高轧制油的润滑、极压抗磨性能对色差的影响
根据现有轧制油的使用情况,通过实验室模拟分析、评价,在轧制油中添加2%的提高轧制油润滑、极压抗磨性能的添加剂,轧制油的皂化值由最初的15.16mgKOH/g提高到17mgKOH/g,最大无卡咬负荷即PB值由原来的490N提高到588N,循环均匀后进行轧制。发现生产0.70mm薄板时轧制力进一步降低,轧制0.63mm薄板时不再有色差出现,轧制0.60mm薄板时也不会有色差出现。
2.3 调整后轧制油使用效果
2.3.1 最小可轧厚度降低情况
使用原来的轧制油一个轧程下只能轧制0.70mm厚的产品,0.60mm以下的薄板需要中间退火一次,采用两个轧程生产。改进后新轧制油可以生产厚度0.60mm的薄板,成品表面无轧制油因素导致的色差、热划伤等质量缺陷,轧制力和以前相比还有大幅度的降低。生产0.60mm厚度以下的产品时可以减少一次中间退火,降低了生产成本,提高了生产效率。
从轧制工艺参数的对比来看,从第二道次开始,各道次的轧制力至少降低6%,第五道次降幅最大达14%,入口、出口张力变化不大,总压下率从73.5%提高至74.5%,工辊凸度从0.25mm降低至0.22mm,辊耗有所降低。8个道次的成品厚度从0.63mm减小至0.60mm。
2.3.2 能耗降低情况
前后收集了1、2轧机轧制0.63mm、0.60mm规格产品的耗电量。
可知:1轧机更换轧制油后8个道次轧制0.6mm的耗电量比更换轧制油前8个道次轧制0.63mm的耗电量降低7.7%左右。2机轧制0.6mm规格成品需两轧程,0.6mm规格的中退料需在第一轧程轧至1.2mm左右,中退一卷19t左右的1.2mm中退料需耗时约1.5h,退火酸洗线的生产成本约4600元/小时,故中退一卷1.2mm中退料需花费7000元左右。由此可见,一卷19t左右的钢卷在1#机上一个轧程直接轧至0.6mm比在2#机上两个轧程轧制可节省成本7000多元。
3、结论
(1)不锈钢薄板生产过程中,原材料的均匀性、辊系缺陷、轧制工艺、润滑状态、轧制油性能等各方面因素都可能导致板面缺陷如色差的产生。
(2)在西南某厂的实际生产过程中通过调整轧制工艺参数和轧制油润滑性能,找到了在偏8辊轧机上生产不锈钢薄板时产生色差的原因及对应的解决办法。
(3)新开发的轧制油使用过程中解决了色差问题,降低了轧制压力,减少一个轧程也可生产薄规格产品,提高了生产效率,降低了生产成本。
文/张旭 孙建林 赵关雄 王士庭
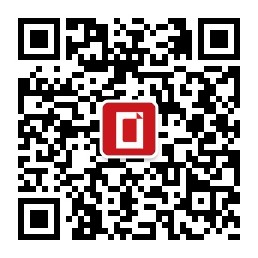