铝镇静钢浇余渣在不锈钢冶炼中的应用研究
- 来源:不锈钢商圈 smarty:if $article.tag?>
- 关键字:电炉,AOD炉,不锈钢 smarty:/if?>
- 发布时间:2015-03-19 08:38
摘要:以降低不锈钢冶炼成本为目的,对不锈钢的冶炼工艺特点及存在的问题进行了阐述;利用铝镇静钢浇余渣高碱度、低熔点的特点,对电炉、AOD炉的冶炼工艺优化后进行了工业性试验。试验表明:铝镇静钢浇余渣能够替换部分石灰,并且能够降低石灰、硅铁、萤石等消耗,同时通过数据分析和对比得出铝镇静钢浇余渣在电炉使用量的合适范围为15~20kg/t,在AOD炉使用量的合适范围为20~30kg/t。该技术的成功应用实现了废弃物的再循环利用,达到了节能减排和降低不锈钢冶炼成本的目的。
关键词:铝镇静钢浇余渣;电炉;AOD炉;不锈钢
引言
电炉和AOD炉(Argon Oxygen Decarburization)作为不锈钢冶炼流程中的关键环节,存在着高能耗和高成本的问题,冶金工作者也在不断进行技术研究和革新来进一步降低两者的冶炼成本。本文根据电炉、AOD炉的冶炼工艺分别于2013年10~12月制定不同的试验方案,成功将铝镇静钢浇余渣进行应用,石灰、硅铁等消耗实现大幅度的降低,实现了废弃物再循环利用,达到了节能减排降成本的目的。
1 铝镇静钢浇余渣的应用原理
1.1 传统的一步法、两步法不锈钢冶炼工艺,在传统意义上“一步法”是指将铁水等进行预处理后兑入AOD炉进行不锈钢的冶炼,“两步法”是指返回物料或铁水经电炉熔炼后再兑入AOD炉进行不锈钢的冶炼。相对来说“一步法”的冶炼工艺综合成本较低,适合于冶炼400系等合金相对较低的不锈钢,而“两步法”中可通过电炉将廉价的低品位物料进行熔炼来缓解AOD炉的热量问题,适合于冶炼300系等合金含量相对较高的不锈钢。但是不论是哪种冶炼工艺,电炉和AOD炉都存在高能耗的问题,故此冶金工作者也在不断进行技术研究和革新来进一步降低两者的冶炼成本。
1.2 电炉冶炼不锈钢工艺简介
电炉冶炼不锈钢与传统的电炉冶炼碳钢冶炼工艺类似,主要分为熔化期、氧化期和还原期。但是,在冶炼过程铬元素不可避免的出现氧化,因所形成的Cr2O3熔点较高导致炉渣黏度增加,发泡和埋弧效果下降,进而发生热效率下降、炉衬砖寿命降低等现象。
通常情况下,为保证电炉冶炼过程中所形成的CaO-SiO2-MgO(7%~9%)-Cr2O3(7%~15%)渣系具有良好地流动性,一般采用降低碱度或增加化渣剂的使用量等方式,但是两种操作模式都会不同程度地增加成本投入和加剧铬元素的损失。
1.3 AOD炉冶炼不锈钢工艺简介
AOD炉冶炼不锈钢过程分为脱碳和还原2个阶段。在脱碳期,主要通过提高熔池温度、降低CO气体分压等方式使碳先于铬进行氧化,即实现“脱碳保铬”;在还原期,主要通过加入硅铁、萤石等脱氧剂和化渣剂将脱碳期所氧化的铬、铁、锰等还原到钢水中,同时兼顾脱气、去除夹杂等任务。
在AOD炉脱碳期由于要加入大量(~300kg/t)的高碳合金和石灰(~120kg/t)致使熔池温度会出现持续性地降低,而根据碳、铬选择性氧化理论和脱碳保铬的温度,在温度降低或不足时就会出现铬优先于碳氧化,而多氧化1%的铬需要额外在脱碳期补加石灰20kg/t,还原期需要多消耗硅铁5.5kg/t、萤石4kg/t,同时在脱碳期补加石灰后又会导致热量不足、温度欠缺,形成硅铁、萤石消耗增加的恶性循环。
池和冰等人的研究并通过冶炼前期加入硅铁等工艺改良,补充脱碳期的热量得到较好效果,但是上述做法都存在一定的费用投入。而如果将脱碳期的部分石灰转移至还原期将会缓解部分热量缺口,但是需要使用价格较高的优质石灰,而普通石灰的质量尤其是灼减理化指标未达到冶炼不锈钢的苛刻要求,石灰中所含的CaCO3不仅在冶炼过程中吸收大量的热量,同时也会造成钢液增碳,对于低成本生产和提升钢液品质极为不利。
1.4 铝镇静钢浇余渣的应用原理
铝镇静钢浇余渣是指在生产铝镇静钢造渣时所产生的一种含55%~60%CaO、5%~10%SiO2的高碱度渣,而此种炉渣在经过熔炼后基本上不含有CaCO3,对于不锈钢来说不会产生增碳现象。同时,铝镇静钢浇余渣又含有25%~30%Al2O3,对于CaO-SiO2-MgO(-Cr2O3)三元(四元)渣系来说,通过调整成分含量均可使炉渣熔点处于低熔点区,在炼钢温度下具有良好的流动性。
如上所述,不论是电炉还是AOD炉在冶炼过程中都存在一定的工艺缺陷和物料条件限制,而铝镇静钢浇余渣虽然是一种废弃炉渣,但是其兼备有效CaO较高、熔点较低、换渣性良好等特点,对于电炉和AOD炉来说均是一种良好的石灰和萤石的替代品。
2 铝镇静钢浇余渣应用方案设计结合铝镇静钢浇余渣的特点,分别针对电炉和AOD炉制定不同的试验方案。
3 试验结果与讨论
3.1 电炉物料消耗量与铝镇静钢加入量关系
随着铝镇静钢浇余渣的加入量增加,石灰的消耗量成下降趋势。因为,铝镇静钢浇余渣中有效CaO高达45.6%,1000kg相当于普通石灰约500kg,具有相当高的替换价值。随着铝镇静钢浇余渣加入量的增加,白云石的消耗增加趋势。这是因为在试验过程中,炉渣碱度仍按照之前低碱度控制,在随渣中Al2O3含量的增加,炉渣的熔点向低熔点区靠近,继而导致炉渣变得更加稀薄,为防止炉衬侵蚀严重增加白云石的消耗。随着铝镇静钢浇余渣加入量的增加,电耗呈现先降低再增加的“V”型趋势。这是因为,在加入量相对较低的炉次,随着加入量增加炉渣黏度降低,炉渣的埋弧效果较好,热效率呈上升趋势。但是在加入量过大时,其有效CaO毕竟只有约45%,替换比较少导致加入量过大额外吸收热量,同时炉渣变得较稀薄,导致钢液在炉内的散热速率增加,电耗呈增加趋势。
3.2 AOD炉各物料消耗与铝镇静钢浇余渣加入量的关系
随着铝镇静钢浇余渣加入量的增加,硅铁消耗呈下降趋势。是因为随着脱碳期石灰量的减少,AOD炉冶炼过程温度的欠缺量得到反向弥补,促使“脱碳保铬”得以顺利进行,形成脱碳期溶液中铬元素氧化量减少的局面,因此硅铁消耗随着铝镇静钢浇余渣的替换量增加呈现出下降趋势。随着铝镇静钢浇余渣加入量的增加,萤石消耗呈现先降低再增加的“V”型趋势。是因为,随着铝镇静钢浇余渣的加入量增加,Al2O3的总量逐渐增加,在Al2O3的作用下渣系的熔点急剧下降,同样属于化渣类的萤石能够得以降低;但是,随着铝镇静钢浇余渣加入量的逐步增大导致钢液和炉渣的温度骤降,在低温下炉渣黏度呈现增加趋势,故在低温下要保持相对较好地流动性需要增加萤石的用量。随着铝镇静钢浇余渣加入量的增加,还原后温度呈现下降趋势,但当超过40kg/t时温度降低速度平缓。是因为,当铝镇静钢浇余渣加入量超过40kg/t时,还原后钢液的温度已基本上低于1600℃,此时炉渣的温度较低,尤其是表层呈现出转变为固态的趋势,炉渣及钢液的传热速度放缓。
4 应用效果及经济效益
根据对试验炉次过程数据的分析和结果的讨论,在2013年12月份基本形成了电炉冶炼过程使用铝镇静钢浇余渣、AOD炉还原期加铝镇静钢浇余渣替代部分石灰的冶炼工艺。同时,在综合硅铁、石灰、萤石消耗、还原后温度等条件后,确定铝镇静钢浇余渣在电炉使用量的合适范围为15~20kg/t,在AOD炉使用量的合适范围为20~30kg/t,在此范围内可降低石灰15~30kg/t、硅铁5~7kg/t、萤石5~7kg/t加入量,吨钢成本降低约55元。
5 结论
(1)通过工业性试验,电炉使用铝镇静钢浇余渣以及AOD炉冶炼过程使用铝镇静钢浇余渣替换部分石灰的工艺是可行的。
(2)综合石灰、硅铁、萤石消耗以及还原后温度的等条件后,铝镇静钢浇余渣在电炉使用量的合适范围为15~20kg/t,在AOD炉使用量的合适范围为20~30kg/t,吨钢成本可降低约55元。
(3)在大力倡导保护环境的今天,应用该项工艺技术不仅能够降低不锈钢的冶炼成本,同时也能够实现废弃资源二次循环再利用,达到节能降耗的目的。
文/雷学东,冯文甫,曹红波
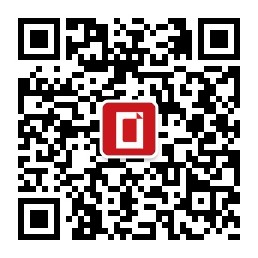