UNS N08904超级奥氏体不锈钢无缝管的生产工艺及性能
- 来源:不锈钢商圈 smarty:if $article.tag?>
- 关键字:UNS N08904,超级奥氏体不锈钢无缝管 smarty:/if?>
- 发布时间:2014-09-15 16:25
摘要:采用冷轧、冷拔、退火处理及酸洗等工艺实现了Φ32mm×7mm规格UNS N08904超级奥氏体不锈钢无缝管的国产化,并对成品管的室温力学性能、晶粒度和晶间腐蚀性能等进行了研究。结果表明:退火处理和酸洗为关键的生产工艺,中间退火工艺为(1060~1100)℃×40min,成品退火工艺为(1040~1080)℃×35min,酸洗液为6%HF+12%HN03,酸洗温度为30~40℃,酸洗时间为15h,在此工工艺条件下成品不锈钢无缝管的各项性能均符合相关标准要求。
关键词:超级奥氏体不锈钢;无缝管;固溶处理;冷轧
引言
UNS N08904超级奥氏体不锈钢属于低碳高镍、铬、钼合金化奥氏体不锈钢,具有良好的抗点蚀和缝隙腐蚀能力、较高的抗应力腐蚀破裂及抗晶间腐蚀能力,在室温和550℃高温下都具有良好的力学性能,此外加工性能和焊接性能良好。
目前,该钢广泛应用于使用温度不超过550℃的工业领域,如硫酸酸洗用加热管、容器、筐及链等,海水冷却热交换器、海洋产品管道系统、酸性气体环境管道,磷酸生产中的热交换器、蒸发器、洗涤、浸渍管等以及石油精炼中的空气热交换器等。此钢常以无缝钢管的形式使用。
UNS N08904超级奥氏体不锈钢无缝管生产技术一直为国外垄断,国内尚未开发出批量生产该类产品的工艺技术。因此,作者所在研发团队结合现有生产设备,对该类产品的生产工艺进行了研究,实现了ф32mm×7mm规格UNS N08904超级奥氏体不锈钢无缝管的国产化,并对其性能进行了分析。
1生产工艺
1.1工艺流程
ф32mm×7mm规格UNS N08904超级奥氏体不锈钢无缝管的生产工艺流程如下:外购荒管→外观尺寸、化学成分检验→酸洗→检验→修磨→冷轧→去脂→热处理→酸洗→冲洗→检验修磨→润滑→烘烤→制头→冷拔→去脂→热处理→矫直→切头→酸洗→冲洗→钝化→冲洗→成品检验→入库。
1.2主要工艺参数
1.2.1冷加工工艺
荒管规格为ф82mm×10.5mm,首先用6%(体积分数,下同)HF和12%HNO3的混合溶液进行酸洗,以去除荒管内外表面的氧化皮,然后人工对荒管进行检验、修磨,以清除荒管内外表面的微细裂纹及表面缺陷;之后在ф9(15~63)mm矫直机上进行管材矫直,矫直直线度不大于2mm·m-1;之后在LG-60型冷轧机上冷轧至规格ф57mm×7.5mm,延伸系数为2.02,冷轧时轧机机架每分钟往返次数为55~65次,单次送进量为3~5mm,避免产生竹节痕及橘皮等冷轧表面缺陷;然后在60t冷拔机设备上经三道次(模具直径分别为48,40,32mm)空拔至成品规格ф32mm×7mm。空拔时的延伸系数在1.2~1.3为宜,在空拔各道次间进行中间退火处理,空拔过程采用慢速冷拔,速度控制在2~4m·min-1,以避免管材表面出现拉拔划痕和造成管材流动变形的不均匀性。成品尺寸符合GB/T14976-2002要求,外径公差±0.3mm,壁厚公差按指定壁厚的±10%控制。
1.2.2退火处理及酸洗工艺
退火处理在UNS N08904超级奥氏体不锈钢无缝管的生产过程中尤为重要,它不仅决定着产品的质量,而且还会影响表面酸洗工艺。中间退火时必须消除内应力和加工硬化,增加管材的塑性,以利于后续加工。成品热处理不仅要消除残余应力和组织缺陷,还要保证材料符合标准要求的力学性能和耐腐蚀性能。采用天然气辊底式连续加热炉对UNS N08904超级奥氏体不锈钢无缝管进行退火处理。产品中间退火温度为1060~1100℃,保温40min,水冷;成品退火温度为1040℃~1080℃,保温35min,水冷。
采用该退火处理工艺可使成品获得较好的质量和酸洗效果。
酸洗主要是为了清除不锈钢表面的氧化皮。不锈钢表面的氧化皮由外到内可分为三层,外层是以氧化铁为主的氧化物;中间层是以四氧化三铁为主的氧化物,且铬镍氧化物也有所增加;内层以铬镍氧化物为主,该层氧化皮较为致密,有部分铁的氧化物(以氧化亚铁为主),酸洗的难度取决于此层氧化皮的结构。由于该管材中含有较高的镍、铬、钼、氮含量,在较低的温度下,尤其是在内层形成的氧化物更为致密,同时钼和氮结合(在较低温度下稳定存在)可显著提高氧化膜的稳定性,增加酸洗难度。所以在生产过程中,适当提高退火处理温度和延长退火时间是很有必要的。另外,在酸洗过程采用了浓度不同于其它奥氏体不锈钢的酸洗液(6%HF+12%HNO3),在30~40℃下浸泡15h,酸洗后成品表面光亮,管材表面的氧化皮彻底清除,且未出现因酸洗而造成的各种缺陷。
2理化检验
按照GB/T20066-2001的规定从荒管和成品钢管上截取试样,按照GB/T11170-2008的要求在GS1000型直读光谱仪上进行化学成分分析。
在3根不同的成品管上截取尺寸为ф32mm×7mm×300mm的拉伸试样,在SHT4106型万能试验机上参考GB/T228-2002进行室温拉伸试验,应变速率为0.002s-1。取20mm长的管段,在HRS-150型洛氏硬度计上进行硬度测试。
工艺性能试验包括压扁试验和扩口试验,试验设备均为SHT4106型万能试验机。压扁试验按照GB/T246-1997的规定进行,试样为ф32mm×7mm×65mm的管段,压扁试验过程分为两个阶段,第一阶段将试样压至两平板间距为16mm,第二阶段继续施压直到试样破裂或内壁相互接触为止。扩口试验在室温条件下按照GB/T242-1997进行,试样为ф32mm×7mm×35mm的管段(2支),试验时采用顶角为60°的圆锥顶头将试样管段的外径扩口40%后观察扩口管段的表面是否有裂纹或开裂;扩口时以5%的扩口率逐级增加,每扩一次后均测表面的硬度和壁厚。
晶粒度检测按照GB/T6394-2002进行,从荒管和成品管上截取长为20mm的管段观察横截面的晶粒度,腐蚀溶液为300mLHCl+500gFeCl3+700mlH2O,腐蚀时间为2s,然后在XJL-03型光学显微镜上进行晶粒度等级评级。
从成品管上切取90mm×10mm×7mm的试样,通过切削的方法除去剪切的影响部分,用洗涤剂去脂并干燥、敏化,然后在腐蚀溶液中进行晶间腐蚀试验。敏化制度:(650±10)℃保温2h后水冷。腐蚀溶液配制:将100g分析纯硫酸铜(CuSO4·5H2O)溶于700ml水+100ml纯硫酸的溶液中,然后稀释至1000ml。将腐蚀溶液及试样置于容量为1L带冷凝器的磨口锥形烧瓶内加热,在烧瓶底部铺一层纯度不小于99.5%的铜屑,微沸腾16h后,取出试样,洗净、干燥、弯曲后进行观察,试样弯2个光面,均弯曲180°。
按GB/T7735和GB/T5777对成品钢管进行超声探伤和涡流探伤,探伤完成后切除两端部盲区150mm。
3理化检验结果
3.1化学成分
荒管和成品管的化学成分分析结果如表1所示。可见,两者的成分十分接近,在整个加工过程中,不存在渗碳,且均符合ASTM-A312《无缝和焊接奥氏体不锈钢公称管》的要求。
表1钢管的化学成分(质量分数%)
3.2力学性能
由表2可见,成品管的室温力学性符合相关标准的规定。
表2成品管的室温力学性能
3.3扩口性能
对比图1,2可见,扩口后管口周围和管材的外表面均未产生明显的裂纹或裂口,说明材料的塑性较好。
图1 成品管扩口前的宏观形貌
图2 成品管扩口40%后的宏观形貌
从图3可以看出,UNS N08904超级奥氏体不锈钢的硬度随着扩口率的增大而增大,但是曲线的斜率随着扩口率的增大逐渐变小,说明材料变形到一定程度后继续增大扩口率,材料的硬化不明显,管端未产生明显的裂纹,材料的塑性较好。从图4可以看出,扩口率与壁厚呈近线性关系,变形率均匀增加,壁厚也在接近均匀的递减。
图3扩口率与硬度的关系
图4扩口率与壁厚的关系
3.4压扁性能
由图5可见,成品管压至上下两边近平行后的横向截面和纵向截面均无裂纹或裂口。
(a)横向截面(b)纵向截面
图5压扁管材截面的宏观形貌
3.5晶粒度
从图6可知,荒管的晶粒度等级为3.5~4级,经冷轧、冷拔、热处理后成品管的晶粒度等级为5.5~6级,晶粒大小均匀。
(a)荒管(b)成品管
图6荒管和成品管的晶粒尺寸
3.6晶间腐蚀性能
从图7可以看出,成品管试样腐蚀并弯曲后的折弯处没有裂纹或其它缺陷,晶间腐蚀性能合格。
图7成品管试样腐蚀并弯曲180°后的宏观形貌
3.7成品管的质量
成品管的涡流、超声波探伤结果符合GB/T7735和GB/T5777的要求。
4结论
(1)采用冷轧和冷拔相结合的工艺,实现了ф32mm×7mm规格UNS N08904超级奥氏体不锈钢无缝管的国产化,其产品尺寸、力学性能和晶间腐蚀性能均符合相关标准要求,钢管内外表面质量优异。
(2)关键的生产工艺为迟火处理与酸洗工艺,中间退火温度为1060~1100℃,保温40min;成品退火温度为1040~1080℃,保温35min;在30~40℃的酸洗液(6%HF+12%HNO3)中浸泡15h的酸洗效果较好。
文/尹显觉 宋祥飞 吴明生 王雅庆
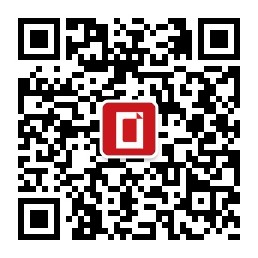