可复制的“传祺”?揭秘广汽乘用车数字化实践
- 来源:国际汽车设计及制造 smarty:if $article.tag?>
- 关键字:揭秘,数字化,实践 smarty:/if?>
- 发布时间:2023-09-03 11:02
文/龚佳枫
截至今年7月,中国汽车产销分别完成1565万辆和1562.6万辆,同比分别增长7.4%和7.9%。其中,新能源汽车产销分别完成459.1万辆和452.6万辆,同比分别增长40%和41.7%,市场占有率达到29%。值得一提的是,截至7月,中国汽车出口253.3万辆,同比增长67.9%,暂时超越日本成为汽车出口第一大国。
随着汽车产业发展进入新常态,“卷”到一定程度的汽车企业,需要进入修炼“内功”、积蓄能力的关键期以超越竞争对手。而在这一过程中,谁能抓住机会更快完成数字化转型升级,谁就能在竞争中掌握主动权。
以广汽传祺为例,其在广州、杭州、新疆、宜昌都设有智慧工厂,以智联化、网联化、共享化为核心,打造了智能技术与解决方案的现代制造质量平台。广汽传祺工厂区别传统模式,以定制化生产模式匹配升级,适应多品种、小批次高度定制化生产。工厂广泛采用基于IoT的视觉应用扩展,通过人工智能+边缘计算,以视觉判断取代人工确认的动作。此外,其还利用数字化同步工程虚拟仿真,实现高品质、高效率、低成本,短周期内完成产品及工艺导入,有效减少产品缺陷,降低运营成本。
配合智能物流和工厂的互联互通,广汽智慧工厂实现了生产自动化、信息&管理数字化和智造生态化,年产能达80万辆,正向着世界级生产方式不断迈进。那么,作为智能制造的先行者,广汽集团的全资子公司广汽乘用车有哪些经验可以供借鉴?又有哪些落地的应用案例分享?本期会客室,我们有幸邀请到广汽乘用车有限公司智能制造专家林郅翔,听他分享广汽传祺多年来在数字化制造的心得和实践成果。
双碳背景下的电气化、智能化转型
作为首家A+H股整体上市的世界500强企业——广汽集团的全资子公司,广汽乘用车打造了消费者熟知的广汽传祺品牌,并且逐步形成了覆盖珠三角、长江经济带和一带一路经济带的大自主生产基地布局,累计投资335亿元,工厂覆盖广州、杭州、宜昌、新疆,年产能约达80万辆。除了整车制造,其业务也辐射到汽车用品、工程技术研发以及动力总成发动机和变速箱产线。
成立于2008年的广汽乘用车在2010年有第一款轿车上市,到2017年实现第100万辆整车下线,两年后就实现第二个百万辆整车下线。2021年,随着传祺系列在中国市场“引爆”,受到年轻客户的喜爱,2022年迎来了第三个百万辆整车下车。可以看到,广汽乘用车在初创阶段也经历了艰难的过程,但其坚持自主研发创新,在技术成熟和产品品质得到市场认可后,销售量得到了较大的飞跃和提升,成为国内知名的汽车品牌。今年5月,广汽乘用车推出了新能源转型的重磅产品——智电新能源E9,该款车型是在现有的M8的基础上改造的,是实现新能源战略目标的一个车型。
广汽乘用车是国内较早研究混动技术的企业,随着技术日渐成熟,百公里油耗在逐渐降低。目前广汽乘用车也是目前唯一拥有双混动技术路线的品牌,其自研的GMC串并联混动系统以及与丰田合作的THS混动系统都经过了10万小时、1,000万公里的有效整车验证,广汽传祺的第四代发动机2.0ATK热效率达到42.1%,刷新了中国品牌发动机最高热效率标准。
当然,广汽在新能源方向转型过程中的努力,不止于推出新款新能源车型。在双碳背景下,广汽集团提出了“NEXT”计划,即New EV+XEV Transition,在多能源时代来临之时,坚持“EV+ICV”(电动化+智能化)“XEV+ICV”(混动化+智能化)双轮驱动路线,力求在保持广汽埃安EV领先优势的基础上,实现广汽传祺向XEV的转型。
广汽集团提出的“NEXT”计划将着力打造能源科技及能源生态、智能科技及出行生态、产业链及产业集群生态三大支撑,以应对汽车行业向“产品+生态”的竞争转变的趋势。“我们在新能源汽车领域的目标是2025年达到全系车型的混动,到2030年混动车型销量占比超过60%,2045年实现碳中和。此外,公司还在加快氢能产品的布局和落地。”林郅翔分享道。
值得一提的是,在智能化方面,广汽乘用车搭载了“星灵”的电子电气架构,该架构是由汽车数字镜像云和中央计算机、智能驾驶计算机、信息娱乐计算机三个核心计算机群组,配以高速以太网、5G、信息安全和功能安全等技术,组成可高效支撑纯电、混动车型的车云一体化集中计算式电子电气架构。相比广汽上一代电子电气架构,“星灵”架构的算力提升50倍,数据传输速率提升10倍,线束缩短约40%,控制器减少约20个。搭载该架构的车型可以拥有超感无忧的智能驾驶和智能交互座舱体验,智能驾驶方面有智能泊车及L2+的智能驾驶辅助,可以满足现在大部分驾驶场景的需求。
广汽的智能制造数字化实践
当前,美国、德国、日本、欧盟、中国等国家和地区都提出了不同的数字化战略,虽然战略愿景以及具体实现的步骤有差异,但最终都指向制造业智能化转型的发展方向。智能制造成为各工业强国发展制造业的方向,促进新生产管理方式、运营模式、产业形态形成,对全球工业格局带来重大影响,第四次工业革命或许就孕育其中。
在这一背景下,广汽乘用车通过大数据、人工智能、区块链等智能制造的技术,打造了以智能制造、智能物流、智能质量和智能服务为核心的生态。以宜昌工厂为例,该工厂是2019年落地建成的,是以世界级的高标准打造的智能标杆工厂,并获得了中国汽车工业科技奖项。宜昌工厂的车间覆盖了冲、焊、涂、总四大工艺,还有发动机变速箱的生产线,达到了生产自动化、信息数字化和管理智能化的水平。另外,其制造生态化、产线柔性化程度也比较高,数据采集的覆盖率达到了96%,可以通过对数据的不断采集分析,对现场生产制造进行指导并解决生产过程中的质量问题。
广汽乘用车的数字化渗透进汽车研产供销全业务流程:从客户下单开始,4S店就会汇总需求,结合现场工艺、库存以及其他限制条件进行排产。在冲、焊、涂、总等制造环节的生产结束下线之后交到质量部进行质检,合格后通过物流运输发回4S店,再交付给客户。此外,数字化在研发设计和供应链环节也会有所助力。例如,整车的供销流程中涉及几十上百个系统,数字化建设是以MES系统为核心,打通了底层的冲、焊、涂、总四大车间的工艺,通过自动化设备对数据进行采集,形成了互联共享分析以及优化,通过数据的挖掘,应用数字仿真技术、视觉可视化平台等,打造智能化的工厂。
林郅翔还给我们分享了几个车间数字化的应用实例。首先是基于IoT的视觉应用扩展,在引入机器视觉以后,通过高精度的视觉识别,采集相关的数据并与MES的虚拟列队进行对比校验,可以判断下线车辆的各种数据是否正确,而以前这一工作是由人工完成的,效率较低,且有更大的判断失误的风险。机器视觉的另一个应用是在电动车尾门的焊接工序中,通过高精度的照片,识别后尾门是否有预留的孔,通过增强、降噪和灰度化等图像预处理,提取相关特征进行模型训练,进行智能化校验,防止不良品流出。“面向未来智能化提升需求,引入视觉技术辅助关键工序来应对多车型高柔性的数字化挑战。”
林郅翔分享的另一个案例是焊接质量的智能预测。“目前,一辆车的焊点有3000多个,这些焊点分布在车上的不同部位,有些位置比较隐秘靠人工难以发现。此外,焊点还需要通过手敲、周期性拆解、超声波检查等环节检测,非要很长的时间和大量的人工去完成,并且无法做到百分百检查。通过现场设备的改造,导入传感器以及焊接机器人,可以对电流电压等数据进行采集、分析处理,再通过大数据AI模型的训练,实现对焊点的智能分析。根据现场焊点的质量情况,可以进行针对性检查,并且能够达到质量全面检测,降低不良品流出率,减少返修成本,整体达到降本增效的效果。”
值得一提的是,广汽乘用车在智能制造数字化领域主要申请的专利有24项,新实用新型专利有14项,发明专利7项,期刊发表17篇,企业的标准有32项,这是数字化部分成果的重要体现。广汽智能数字化的应用不仅促进了产能效益的快速落地,也广泛获得了包括中国汽车工程学会、中国设备协会等社会各界的广泛认可及荣誉,相信未来,通过数字化、智能化的转型,广汽能够带给消费者更多的惊喜!
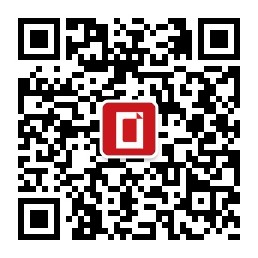