四合一 快速车削工具
- 来源:发明与创新·中学生 smarty:if $article.tag?>
- 关键字:车削工具 smarty:/if?>
- 发布时间:2014-05-09 09:03
职业院校竞赛加工零件过程中,由于受到加工时间及加工质量的限制,原有工具及加工方法不能满足竞赛要求。为此,我设计了本作品,力求达到加工时间最短、加工效率最高。本作品不仅适用于竞赛,也适合企业的单件小批量生产使用。
一、性能特点
1.套丝
使用原有工具时,操作困难,容易倾斜。首先将装好板牙的板牙架的一端杆搭在机床一处,再转动尾座手轮,使尾座端面轻轻靠住板牙架端面,整个过程非常繁琐。而且用这种方法支撑板牙,非常不可靠,板牙架容易歪,影响装置的套丝效果,出现乱牙现象。
而四合一快速车削工具操作简单,并能保证垂直。基体连接部的外壁与活动导套的内壁之间存在间隙,可浮动调节,能保证工件轴线与板牙轴线自动重合,使套丝效果较佳,不出现乱牙现象。
2.钻孔
使用原有工具移动尾座,操作时间长。拧松钻夹头,直接更换麻花钻,此种更换方式在重新安装麻花钻时对钻孔深度不宜掌控。
有了四合一快速车削工具就可不移动尾座,使操作时间变短。需要更换麻花钻时,只要换上新的钻孔模块,就能掌控钻孔的深度,简单方便,省时省力,还提高了钻孔效率。
3.铰孔
使用原有工具移动尾座,操作时间长,无浮动调节。将铰刀和钻夹头整套更换时先摇动车床尾座手轮,使钻夹头的锥柄从车床尾座的锥孔中顶出,然后重新装入一套铰刀和钻夹头。此更换方式过程较繁琐,费时费力,影响铰孔的效率。
而四合一快速车削工具操作方便,可浮动调节。需更换铰刀时,只要换上新的铰孔模块,就能控制铰孔深度,更换过程简单方便,省时省力,提高了铰孔的效率。
4.攻丝
使用原有工具丝锥容易折断,操作不方便。
且对丝锥没有任何过载保护措施,一旦遇到被攻材料过硬等情况时,容易折断丝锥,不仅报废工件,也影响加工效率,增加生产成本。
使用四合一快速车削工具后丝锥不易折断,操作方便。丝锥安装在过载保护攻丝夹头内,当力扭矩超过正常值时进行过载保护,使丝锥停止进给,使其不被折断,提高加工效率,减少生产成本。
二、作品优点
1.快速装拆及加工,提高效率。本作品最主要的创新点是,将四种加工方式集合在一起,实现一套工具完成四种加工。
同时,将不同功能进行模块化设计,通过基体及模块化结构配合,实现快速装拆。基体主体结构是莫氏锥柄,装在车床尾座以实现定位及装夹功能。
钻孔、铰孔、攻丝、套丝四种模块可便捷、快速与基体配合,实现四种加工。由于基体锥柄通过尾座与机床实现固定位置关系,再通过基体上的止动销与定位槽实现四种模块的快速装夹与定位。
本作品利用车床尾座,以一个锥柄为主要结构体,设计、加工和采购一组适合钻孔、铰孔、攻丝、套丝的标准互换体。同时刻有刻度线,便于控制长度。
在进行车削加工时,按不同加工类型进行模块组合,实现加工零件一次装夹,完成钻孔、铰孔、攻丝、套丝的全过程。
2.自动找正及过载保护功能。本作品在铰孔、攻丝、套丝过程中通过导套与基体之间的间隙配合,实现浮动自动找正。攻丝时通过过载保护夹头,实现过载保护,防止丝锥断在工件内。
3.基体上设计排气及排屑孔(同一个孔),不仅方便不同模块更换时内腔气体的排出,更解决了加工中排屑难的问题,气体可通过排屑孔吹进基体内腔,并将切屑从前端吹出。
4.提高了加工效率。一般情况下,完成钻孔、铰孔、攻丝只需3至5分钟,且对操作者的技能和熟练度要求不高,而采用原有加工方式至少需要10分钟。
5.提升了加工质量。采用原有加工方式铰孔时,铰刀可能由于与工件轴线不对正,导致铰孔质量不佳或者铰刀折断。而本作品采用浮动方式让铰刀自动找正,保证铰孔质量。
在攻丝时丝锥不好找正易导致螺纹歪斜及丝锥折断,采用本作品加工通过尾座定位、浮动找正及过载保护,能确保螺纹正直且丝锥不会折断;在套丝时与前两者一样也能确保螺纹正直。6.性价比高,节约成本。相比原有加工方式需要的工具,本作品只需在原有基础上加工几个标准零件及采购过载保护攻丝夹头,成本增加了约一百元。采用标准互换模块零件方便在模块零件磨损或损坏时进行替换,而不需要整体更换,节约了成本。
相比增加的一百元成本,加工提高的效率和质量所取得的效益要大得多,所以本产品在育才机械厂等企业试用后取得了良好的经济效益,受到了企业的欢迎。
王爱国
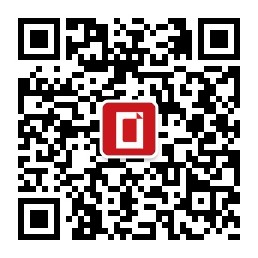