MTA生产模式构建快速消费品生产企业的竞争优势
- 来源:AMT《前沿论丛》 smarty:if $article.tag?>
- 关键字:MTA,生产模式,快速消费品,竞争 smarty:/if?>
- 发布时间:2011-06-30 13:05
在快速消费品行业中,产品良好的可得性是消费者的重大需求。然而分析发现,大多数快速消费品生产企业所宣称的按库存生产只是“伪”库存生产模式,更贴切地说是按预测生产,但是预测通常都不是很准确。MTA生产模式是一种拉动式的快速补货方式,使用缓冲库存的概念来保护企业的销售增长。
食品、饮料、白酒等快速消费品行业的一个显著特点是:顾客为取得所需货品等待时间接近于零。良好的可得性是消费者的重大需求,而期望买到某个商品却因为缺货不得不转购买其他替代商品,或者失望而归会大大伤害消费者对良好可得性的印象。
很显然,快速消费品行业必须靠提前生产来预备一定的库存量而不是接到顾客的需求后才安排生产,即我们常说的按库存生产模式(Make-to-stock),简称MTS生产。
但经过实际分析发现,大多数的快速消费品生产企业所宣称的按库存生产只是“伪”库存生产模式。为什么这么说呢?让我们看看最核心的启动生产的触发信号机制是:销售人员的预测。销售人员会根据去年或者几个月的历史销售数据来预测下几个月要生产的产品数量和清单(但愿上帝保佑销售人员预测正确,否则只能产生两种后果,一是库存太多,二是库存太少)。我们再来看看其操作流程:当销售人员接到客户的订单时,首先会看看库存是否足够满足客户的需求,如果不够或没有库存,则会和生产计划人员沟通并要求其尽快安排生产补货。这里需要注意的是所谓“客户订单”,在我们所服务的一些企业里面,发现很多客户订单只是明确了数量而未明确交期,客户说“你先生产出来吧,具体交货待我通知后再发货”。客户为什么这样做?因为客户被企业过往不能做到准时交货的不良表现伤害了,出于安全考虑而被迫采取提前下达订单的方式。客户下达订单的依据是什么?预测!
因此,我们说很多企业的生产模式只是“伪”库存生产,更贴切的说法应该是按照预测生产(Make-to-forecast)。
显而易见,预测都是不准确,即使你用再精准复杂的预测计算模型也无法做到百分之一百的准确性。可口可乐的中国生产工厂太古可乐有限公司曾经花费数百万元开发了一套复杂的预测计算模型工具,其准确度也仅能达到70%。
但大多数公司的典型做法就是每个月25号左右开始预测下个月做什么, 花上将近一个星期的时间去收集各方面的信息,并在月初如2号左右开始提交生产计划,这种复杂的计划过程导致了很多人不愿意频繁地做生产计划,而现实中客户的实际需求和计划又不一样。这时候,一定会产生两种结果,要么库存太高,要么库存太少。这种来自市场的压力通常会打乱原来安排好的计划,损失掉宝贵的产能,产生了一堆的紧急订单,带给现场的只有“混乱”两个字。很显然,靠预测来启动生产并不能确保我们要货有货,并不能帮助我们实现顺畅的生产,而在传统的MTS的概念里,有谁对“要货有货”负责吗?没有,最后受伤害的是客户以及公司的增长机会。
“企业的生产、采购以不准确的销售需求做驱动”是关键问题所在。那么,如何解决这一关键问题呢?企业通过增强销售预测的准确性无法从根本上解决问题,必须改变以往以预测做生产驱动的模式,采用MTA((Make to Availability)的生产模式,即为可得性而生产。
什么是MTA的生产模式呢?
标准的MTA生产模式的定义是:一种对市场的承诺,或对特定客户的承诺,在特定的仓库维持足够的可得性 (足够的产品数量),使能在收到需求后立即出货达交。
用更简单明了的描述,我们可以这样理解: “我们不再基于预测安排生产,而是设定适当的缓冲库存来确保100%的要货有货,然后通过实际的库存消耗来快速补货并动态调整缓冲库存水准。”
MTA生产模式是使用缓冲库存(stock buffer)的概念来保护企业的销售增长,其目的就是要确保接近100%的最高客户服务水准。 MTA对市场的承诺是100%的要货有货,并且不能产生太多没必要的库存,而MTA启动生产的触发信号是什么? 那就是每天库存缓冲的销售数据,每天来自中央仓库的消耗数据就是启动生产信号的输入信息,在MTA的环境下,我们直接使用消耗数据来间接取代预测在传统生产模式中的作用。在MTA的机制下,必须要求紧密监督市场销售数据的变化和中央仓库每个产品的消耗状况,而生产部门也必须根据各个产品的库存缓冲状况来安排生产计划和优先顺序,不仅仅是把产品做出来那么简单了,因为也必须对每个产品的可得性负责了。
MTA生产模式是一种拉动式的快速补货方式,有别于传统的推动式生产计划方式。根据部分已实施了MTA生产模式的企业运作状况来看,MTA生产模式在没有增加任何大的投资和费用的前提下,可以在短短的几个月甚至几个星期内取得重大改善成果:库存周转率提升一倍以上;准时交货率可达99%以上;可释放出30%以上的有效产能。同时,毋庸置疑,通过对市场100%的可得性承诺,企业能获取更高的销售增长机会,占据更大的市场份额。
实施MTA生产模式的几个关键要点:
1. 如何建立合理的缓冲库存并动态调整?
缓冲库存=补货期间内平均库存消耗量 + 安全库存量
举例来说,如果一个产品的生产补货周期为1周,则该产品的缓冲库存应该等于1周内的平均库存消耗量加上安全库存量。为什么要加上安全库存量呢?因为产品的库存消耗并非是均衡的,总会存在起伏波动,通过安全库存量的设置可以保护一些不可控因素带来的不确定性。安全库存量的计算可根据产品绝对偏差平均值(MAD)和安全因子来得到。比如,我们可根据下表产品A的历史库存消耗数据得到其MAD为200。
产品 A
第几周 实际库存消耗量 平均库存消耗量 偏差 偏差绝对值
1 1200 1000 +200 200
2 800 1000 -200 200
3 600 1000 -400 400
4 1300 1000 +300 300
5 900 1000 -100 100
6 800 1000 -200 200
7 1000 1000 0 0
8 1400 1000 +400 400
9 1100 1000 +100 100
10 900 1000 -100 100
总计 10000 2000
平均库存消耗量=10000÷10=1000
MAD=2000÷10=200
安全因子则与所期望达到的服务水平相关,比如98%的服务水平则表示允许容忍2%的缺货率。正态分布下的安全因子表如下:
服务水平(%) 安全因子(使用平均绝对偏差)
50.00 0.00
75.00 0.84
80.00 1.05
84.13 1.25
85.00 1.30
89.44 1.56
90.00 1.60
93.32 1.88
94.00 1.95
94.52 2.00
95.00 2.06
96.00 2.19
97.00 2.35
97.72 2.50
98.00 2.56
98.61 2.75
99.00 2.91
99.18 3.00
99.38 3.13
99.50 3.20
99.60 3.31
99.70 3.44
99.80 3.60
99.86 3.75
99.90 3.85
99.93 4.00
99.99 5.00
如果期望达到的服务水平为99.99,则安全库存量=MAD×安全因子=200×5=1000。
产品A的缓冲库存=补货期间内平均库存消耗量 + 安全库存量 = 1000+1000=2000。
实际上,缓冲库存并非设定好以后就固定不变,在MTA生产模式下,采取动态缓冲管理(Dynamic Buffer Management,DBM)的方法来调节缓冲库存量。一般会将缓冲库存按照三份之一的量划分为三个层级,并以三种颜色标识,如下图所示:
当库存消耗至缓冲库存的67%~100%之间时,则落在绿区;当库存消耗至缓冲库存的33%~67%之间时,则落在黄区;当库存消耗至缓冲库存的0%~33%之间时,则落在红区。
如果在实际生产运作中发现库存经常出现在黄区或红区时,则表示缓冲库存的制定可能有问题, 需要适当地调高缓冲库存(调节的时候一般按原有缓冲库存的1/3增加)。同样的道理,如果在实际生产运作中发现库存经常出现在绿区时,则需要适当的调低缓冲库存(调节的时候一般按原有缓冲库存的1/3减少)。
2. 如何确定生产的优先顺序?
在MTA环境下,“缓冲状态是确定生产优先顺序的唯一标准”。
如上所述,我们通过动态缓冲管理把库存设置为三个颜色区域,当库存落在红色区域时,则表示可用的缓冲库存快要被消耗殆尽了,需要优先赶工生产,其次应生产落在黄色区域的产品,最后才生产落在绿色区域的产品。
但是,如果同时有两个产品都落在红色区域的时候,应该先生产哪个产品呢?这时候,我们就需要用缓冲状态来确定生产的优先顺序了。
缓冲状态= (缓冲库存-目前剩余库存)÷ 缓冲库存×100%,缓冲状态值越大则表示生产优先级别越高。
范例:
假设现在有两张生产补货订单:
一张补货订单要生产 500 个A 产品,缓冲库存是1000 个,在库存货有 430 个。
一张补货订单要生产 100 个B 产品,缓冲库存是 300 个,在库存货有 106 个。
A产品的缓冲状态=(1000-430)/1000*100%=57%
B产品的缓冲状态=(300-106)/300*100% = 65%
则生产的优先级别为:先生产B产品,再生产A产品。
3. 善用MTA环境下的保护性产能
在MTA环境下,企业能感受到波动的市场需求,特别是对于有淡旺季特征的产品而言更加明显。当需求突然增加,缓冲库存会被快速消耗。因此,为确保产品之可得性,需要立即生产来补充其缓冲库存。
同时,由于采取了MTA的生产模式,企业产品的可得性增高,会使得销售增加。由于生产必须能快速回应所有需求增加的情形,它必须维持足够的保护产能。换一种说法就是,生产必须不投入它全部的产能,而是有一些保留。
生产上的负荷与依照承诺而可靠达交之间,存有某种关联性。当负荷低于80%时,要做到对任何承诺准时达交,其中的问题很少。当负荷超过80%之界线时,麻烦的程度开始往上攀升。当超过90%时,难度急遽上升。当超过100%时,绝没办法依照承诺准时达交。
因此,为了迎合突然增加的市场需求,建议拥有大约20%的保护产能,并绝不要低于10%。这样意味着即使有紧急需求或客户需求上升时我们也有办法去临时应付。那么预留这20%是不是浪费呢? 我们可以在需求没有增加时,利用这部分预留的20%产能去生产那些未来能卖出的标准产品,但当市场需求增加时,则应该迅速切换来快速生产以补充缓冲库存。
作者:杨宁 AMT高级咨询顾问
关键字:MTA 生产模式 快速消费品
……
食品、饮料、白酒等快速消费品行业的一个显著特点是:顾客为取得所需货品等待时间接近于零。良好的可得性是消费者的重大需求,而期望买到某个商品却因为缺货不得不转购买其他替代商品,或者失望而归会大大伤害消费者对良好可得性的印象。
很显然,快速消费品行业必须靠提前生产来预备一定的库存量而不是接到顾客的需求后才安排生产,即我们常说的按库存生产模式(Make-to-stock),简称MTS生产。
但经过实际分析发现,大多数的快速消费品生产企业所宣称的按库存生产只是“伪”库存生产模式。为什么这么说呢?让我们看看最核心的启动生产的触发信号机制是:销售人员的预测。销售人员会根据去年或者几个月的历史销售数据来预测下几个月要生产的产品数量和清单(但愿上帝保佑销售人员预测正确,否则只能产生两种后果,一是库存太多,二是库存太少)。我们再来看看其操作流程:当销售人员接到客户的订单时,首先会看看库存是否足够满足客户的需求,如果不够或没有库存,则会和生产计划人员沟通并要求其尽快安排生产补货。这里需要注意的是所谓“客户订单”,在我们所服务的一些企业里面,发现很多客户订单只是明确了数量而未明确交期,客户说“你先生产出来吧,具体交货待我通知后再发货”。客户为什么这样做?因为客户被企业过往不能做到准时交货的不良表现伤害了,出于安全考虑而被迫采取提前下达订单的方式。客户下达订单的依据是什么?预测!
因此,我们说很多企业的生产模式只是“伪”库存生产,更贴切的说法应该是按照预测生产(Make-to-forecast)。
显而易见,预测都是不准确,即使你用再精准复杂的预测计算模型也无法做到百分之一百的准确性。可口可乐的中国生产工厂太古可乐有限公司曾经花费数百万元开发了一套复杂的预测计算模型工具,其准确度也仅能达到70%。
但大多数公司的典型做法就是每个月25号左右开始预测下个月做什么, 花上将近一个星期的时间去收集各方面的信息,并在月初如2号左右开始提交生产计划,这种复杂的计划过程导致了很多人不愿意频繁地做生产计划,而现实中客户的实际需求和计划又不一样。这时候,一定会产生两种结果,要么库存太高,要么库存太少。这种来自市场的压力通常会打乱原来安排好的计划,损失掉宝贵的产能,产生了一堆的紧急订单,带给现场的只有“混乱”两个字。很显然,靠预测来启动生产并不能确保我们要货有货,并不能帮助我们实现顺畅的生产,而在传统的MTS的概念里,有谁对“要货有货”负责吗?没有,最后受伤害的是客户以及公司的增长机会。
“企业的生产、采购以不准确的销售需求做驱动”是关键问题所在。那么,如何解决这一关键问题呢?企业通过增强销售预测的准确性无法从根本上解决问题,必须改变以往以预测做生产驱动的模式,采用MTA((Make to Availability)的生产模式,即为可得性而生产。
什么是MTA的生产模式呢?
标准的MTA生产模式的定义是:一种对市场的承诺,或对特定客户的承诺,在特定的仓库维持足够的可得性 (足够的产品数量),使能在收到需求后立即出货达交。
用更简单明了的描述,我们可以这样理解: “我们不再基于预测安排生产,而是设定适当的缓冲库存来确保100%的要货有货,然后通过实际的库存消耗来快速补货并动态调整缓冲库存水准。”
MTA生产模式是使用缓冲库存(stock buffer)的概念来保护企业的销售增长,其目的就是要确保接近100%的最高客户服务水准。 MTA对市场的承诺是100%的要货有货,并且不能产生太多没必要的库存,而MTA启动生产的触发信号是什么? 那就是每天库存缓冲的销售数据,每天来自中央仓库的消耗数据就是启动生产信号的输入信息,在MTA的环境下,我们直接使用消耗数据来间接取代预测在传统生产模式中的作用。在MTA的机制下,必须要求紧密监督市场销售数据的变化和中央仓库每个产品的消耗状况,而生产部门也必须根据各个产品的库存缓冲状况来安排生产计划和优先顺序,不仅仅是把产品做出来那么简单了,因为也必须对每个产品的可得性负责了。
MTA生产模式是一种拉动式的快速补货方式,有别于传统的推动式生产计划方式。根据部分已实施了MTA生产模式的企业运作状况来看,MTA生产模式在没有增加任何大的投资和费用的前提下,可以在短短的几个月甚至几个星期内取得重大改善成果:库存周转率提升一倍以上;准时交货率可达99%以上;可释放出30%以上的有效产能。同时,毋庸置疑,通过对市场100%的可得性承诺,企业能获取更高的销售增长机会,占据更大的市场份额。
实施MTA生产模式的几个关键要点:
1. 如何建立合理的缓冲库存并动态调整?
缓冲库存=补货期间内平均库存消耗量 + 安全库存量
举例来说,如果一个产品的生产补货周期为1周,则该产品的缓冲库存应该等于1周内的平均库存消耗量加上安全库存量。为什么要加上安全库存量呢?因为产品的库存消耗并非是均衡的,总会存在起伏波动,通过安全库存量的设置可以保护一些不可控因素带来的不确定性。安全库存量的计算可根据产品绝对偏差平均值(MAD)和安全因子来得到。比如,我们可根据下表产品A的历史库存消耗数据得到其MAD为200。
产品 A
第几周 实际库存消耗量 平均库存消耗量 偏差 偏差绝对值
1 1200 1000 +200 200
2 800 1000 -200 200
3 600 1000 -400 400
4 1300 1000 +300 300
5 900 1000 -100 100
6 800 1000 -200 200
7 1000 1000 0 0
8 1400 1000 +400 400
9 1100 1000 +100 100
10 900 1000 -100 100
总计 10000 2000
平均库存消耗量=10000÷10=1000
MAD=2000÷10=200
安全因子则与所期望达到的服务水平相关,比如98%的服务水平则表示允许容忍2%的缺货率。正态分布下的安全因子表如下:
服务水平(%) 安全因子(使用平均绝对偏差)
50.00 0.00
75.00 0.84
80.00 1.05
84.13 1.25
85.00 1.30
89.44 1.56
90.00 1.60
93.32 1.88
94.00 1.95
94.52 2.00
95.00 2.06
96.00 2.19
97.00 2.35
97.72 2.50
98.00 2.56
98.61 2.75
99.00 2.91
99.18 3.00
99.38 3.13
99.50 3.20
99.60 3.31
99.70 3.44
99.80 3.60
99.86 3.75
99.90 3.85
99.93 4.00
99.99 5.00
如果期望达到的服务水平为99.99,则安全库存量=MAD×安全因子=200×5=1000。
产品A的缓冲库存=补货期间内平均库存消耗量 + 安全库存量 = 1000+1000=2000。
实际上,缓冲库存并非设定好以后就固定不变,在MTA生产模式下,采取动态缓冲管理(Dynamic Buffer Management,DBM)的方法来调节缓冲库存量。一般会将缓冲库存按照三份之一的量划分为三个层级,并以三种颜色标识,如下图所示:
当库存消耗至缓冲库存的67%~100%之间时,则落在绿区;当库存消耗至缓冲库存的33%~67%之间时,则落在黄区;当库存消耗至缓冲库存的0%~33%之间时,则落在红区。
如果在实际生产运作中发现库存经常出现在黄区或红区时,则表示缓冲库存的制定可能有问题, 需要适当地调高缓冲库存(调节的时候一般按原有缓冲库存的1/3增加)。同样的道理,如果在实际生产运作中发现库存经常出现在绿区时,则需要适当的调低缓冲库存(调节的时候一般按原有缓冲库存的1/3减少)。
2. 如何确定生产的优先顺序?
在MTA环境下,“缓冲状态是确定生产优先顺序的唯一标准”。
如上所述,我们通过动态缓冲管理把库存设置为三个颜色区域,当库存落在红色区域时,则表示可用的缓冲库存快要被消耗殆尽了,需要优先赶工生产,其次应生产落在黄色区域的产品,最后才生产落在绿色区域的产品。
但是,如果同时有两个产品都落在红色区域的时候,应该先生产哪个产品呢?这时候,我们就需要用缓冲状态来确定生产的优先顺序了。
缓冲状态= (缓冲库存-目前剩余库存)÷ 缓冲库存×100%,缓冲状态值越大则表示生产优先级别越高。
范例:
假设现在有两张生产补货订单:
一张补货订单要生产 500 个A 产品,缓冲库存是1000 个,在库存货有 430 个。
一张补货订单要生产 100 个B 产品,缓冲库存是 300 个,在库存货有 106 个。
A产品的缓冲状态=(1000-430)/1000*100%=57%
B产品的缓冲状态=(300-106)/300*100% = 65%
则生产的优先级别为:先生产B产品,再生产A产品。
3. 善用MTA环境下的保护性产能
在MTA环境下,企业能感受到波动的市场需求,特别是对于有淡旺季特征的产品而言更加明显。当需求突然增加,缓冲库存会被快速消耗。因此,为确保产品之可得性,需要立即生产来补充其缓冲库存。
同时,由于采取了MTA的生产模式,企业产品的可得性增高,会使得销售增加。由于生产必须能快速回应所有需求增加的情形,它必须维持足够的保护产能。换一种说法就是,生产必须不投入它全部的产能,而是有一些保留。
生产上的负荷与依照承诺而可靠达交之间,存有某种关联性。当负荷低于80%时,要做到对任何承诺准时达交,其中的问题很少。当负荷超过80%之界线时,麻烦的程度开始往上攀升。当超过90%时,难度急遽上升。当超过100%时,绝没办法依照承诺准时达交。
因此,为了迎合突然增加的市场需求,建议拥有大约20%的保护产能,并绝不要低于10%。这样意味着即使有紧急需求或客户需求上升时我们也有办法去临时应付。那么预留这20%是不是浪费呢? 我们可以在需求没有增加时,利用这部分预留的20%产能去生产那些未来能卖出的标准产品,但当市场需求增加时,则应该迅速切换来快速生产以补充缓冲库存。
作者:杨宁 AMT高级咨询顾问
关键字:MTA 生产模式 快速消费品
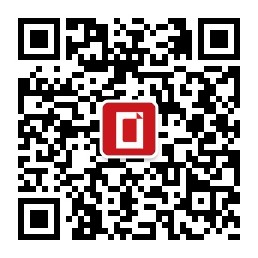